- Team Associated T4.2 - Tony Phalen - Build -
Page 1
The Build – Part 5 - Shocks
The shocks are up next, and Team Associated is well known for having some of the best shocks in the industry. The Factory Team T4.2 comes with the A-Team’s 12mm Big Bore shocks complete with bottom load seals and bleeder caps. You can’t get much better than this in 1/10th scale!
Build Notes:
* You will be filling the shocks with shock fluid and, of course, bleeding them so it is suggested that you have some paper towels handy for clean up.
 Step 79 -
The shock pistons have a small number molded into them (1.6, 1.7 etc), but they are extremely hard to see. To make them a little easier, I used a Sharpie to color the area over the number. For this build, I’ll be using the stock shock pistons per the manual (1.6 front, 1.7 rear). Sorry for the blurry pic.
 Step 80 -
Snap an e-clip into the lower groove on the shock shaft followed by the shock piston. Secure with the 2nd e-clip. Make sure you put the 1.6 pistons on the shorter shafts and the 1.7 pistons on the longer shafts.
 Step 81 -
We will be putting down-travel limiters on the shafts, 4 on each front shaft and 2 on each rear shaft.
 Step 82 -
Grab your shock bodies and slide one of the small, black o-rings over the shock seal opening as shown. As you can see, we’ve prepped the pieces to install in the shock seal area.
 Step 83 -
Time to build the lower seals. I like to put them on a tool so that I can lube up the parts without making too much of a mess. Take any driver (preferably one that is smaller than the holes in the parts) and start by installing a shock hat bushing (make sure the lip is facing INTO the shock body) followed by ared o-ring, shock spacer, red o-ring and then another shock hat bushing (make sure, with this one, the lip is facing AWAY from the shock body). Apply a drop of two of shock oil and make sure all the parts are well lubricated.
 Step 84 -
Insert the parts into the lower area of the shock and make sure they all seat properly. Attach the lower shock cap, making sure to align the hole in the cap with the lip on the shock hat bushing. Tighten all the way down.
 Step 85 -
Put an additional drop of shock oil on the threads of the shaft. Yes, another blurry pic…but at least the shock body is in focus.
 Step 86 -
Slide the shock shaft assembly into the body (make sure you put the shorter, front shafts into the shorter, front shock bodies) and slide it down through the seal assembly. The shock oil allows the shaft’s threads to pass through the seals without tearing them. Now install a shock eyelet on each of the 4 shocks, screwing them on to the top of the threads. Be careful when holding the shock shaft that you don’t scratch it when installing the eyelet. I use a pair of STRC’s shock holding pliers. Great tool; holds tight, doesn’t scratch the shock shaft.
 Step 87 -
Pop one of the Factory Team pivot balls into each of the eyelets. I suggest doing this on a solid surface…it just makes it easier. I used the side of my needlenose pliers.
 Step 88 -
Wrap one of the larger o-rings onto the top of each shock as shown.
 Step 89 -
Pull the shaft down (so the piston sits at the bottom of the shock) and fill it with oil to ALMOST the top. Slide the shock shaft up and down so the oil can filter through the piston and fill up the bottom of the shock (under the piston). Doing this, you will see the air bubbles rise to the top. You want to get rid of all of these bubbles.
 Step 90 -
Place your shocks in a shock stand for about 5 minutes. This will allow all the air bubbles to rise to the top. I use on of Team Fast Eddy’s shock stands to hold mine. This shock stand has holes to fit 1/10th, 1/8th and 1/5th scale shocks. Once the bubbles are gone, refill the shocks to the top.
 Step 91 -
GO WASH YOUR HANDS WITH SOAP! I can’t emphasize this enough. You will be inserting the other larger o-rings into the grooves of the shock collars and if your hands have oil on them, it can make this a very frustrating task. It takes 20 seconds…go do it. I’ll wait.
 Step 92 -
Now that you have clean hands (and your shock collars are built), we’ll move on. Take one of the 2x4mm screws, slide a shock cap o-ring onto it and feed it into the shock cap hole. Tighten down a bit, but not all the way. Build 4 caps.
 Step 93 -
Take your shock cap and put a drop or two of shock oil into it. Now, flip it over and screw it down onto the shock. Be extremely careful that the black o-ring (on the top part of the shock body) fits UNDER the shock cap when you tighten it down. If it ‘squeezes’ out the side of the cap, the assembly won’t seal and you’ll have a leaky shock. Build 4 shocks.
 Step 94 -
Now loosen up the shock cap screw and slowly push the shock shaft up. You’ll see some oil come out of the shock cap hole. When the shaft is to the top, tighten the shock cap screw. Do not overtighten as you need the red o-ring to seal the hole. Do this to all 4 shocks.
 Step 95 -
Another view of your sealed shock cap.
 Step 96 -
Once the caps are on and secure, thread the shock collars onto all 4 shocks…
 Step 97 -
…followed by a spring and the lower spring retainer cup. Make sure you put the shorter springs on the front shocks and the longer springs on the rear shocks.
 Step 98 -
Attach the top of the front shocks to the tower and secure with the shock mount nut. Do not overtighen; you want the shock to have a little bit of wiggle.
 Step 99 -
Slide the lower part of the front shock into the gap in the front suspension arm. Attach (in the outside hole) with the 4-40 screws. Do this on both sides (and make sure both lower mounting positions are in the same hole).
 Step 100 -
Attach the top of the rear shocks to the tower like you did with the fronts.
 Step 101 -
Using the 4-40 screw, attach the bottom of the shocks to the rear suspension arms. Make sure both sides use the inside mounting hole.
The Build – Part 6 - Electronics
The next step involves installing the electronic gear. As mentioned before in the build Table of Contents, we’ll be using a Team Associated XP DS131 steering servo, LRP Flow brushless ESC, Reedy Sonic 17.5 brushless motor and a Reedy WolfPack LiPo battery. Vintage car with current technology…a winning combo!
Build Notes:
* No real tricks involved with this step other than making sure you solder the wires onto the motor in the correct sequence; A wire to A tab on the motor, B wire to B tab, etc.
 Step 102 -
First we’ll install the XP DS1313 servo. AE has included different servo horns for a variety of servos, so make sure you choose the one that is designed for your servo. Fit the ballend to the servo horn as shown, then install the blue expansion ring. Finally, attach the servo horn assembly to your servo, making sure the servo horn is just slightly off 90 degrees (see manual). You’ll be using the screw that came with your servo to secure the horn.
 Step 103 -
Attach the servo mounts to the servo as shown, but do not tighten the screws yet. You can use the Servo Chart on page 17 of the manual to figure out which spacers to use.
 Step 104 -
If you tightened down the servo mounts in step 103, the holes for mounting to the chassis may not line up when you install the servo assembly into the chassis. If you loosen them up and re-install, you’ll see that you won’t be able to tighten them once it’s in the chassis. The fix? Simply mount the servo to the BOTTOM of the chassis first! Line up the holes in the chassis, insert the 4-40×3/8 screws from the other side and snug down. Now tighten the servo mount screws. Remove the 2 screws attaching the assembly to the chassis, flip the servo to the inside of the chassis and secure with the 2 4-40 screws again. The holes will line up perfectly!
 Step 105 -
See, a perfect fit without driving you crazy trying to tighten up the servo mount screws.
 Step 106 -
Build the servo link assembly per the instructions…
 Step 107 -
…and pop into place between the servo horn and the steering system.
 Step 108 -
Slide your motor into place at attach to the motor mount using the M3 screws. Don’t forget the washers. Do not tighten all the way down yet.
 Step 109 -
Slide your pinion on the motor shaft and align it with the spur gear. Make sure there is complete tooth contact, then tighten down the pinion’s setscrew to secure. You’ll also want to set the gear mesh at this point. Page 18 in the manual has good instructions on how to do this.
 Step 110 -
Attach the gear cover to the motor mount as shown and pop the dust cover button into place. I lost the 2 4-40 screws used in this step but thankfully have some blue, Factory Team ones to replace them.
 Step 111 -
Tape your receiver and ESC into place as shown, slightly behind the channel running across the middle of the chassis. Try and get them as close to the center as possible for better weight distribution. Feed the ESC power lead through the slits in the chassis, resting it in the channel. Plug it in to the receiver.
 Step 112 -
This ESC power lead will move around a bit, so I usually tape it into place to secure it. This is also a good time to plug the servo lead into the receiver and mount the ESC switch.
 Step 113 -
Run the receiver antenna down through the chassis and back up through the hole. Feed it into the antenna tube and press the antenna tube into the chassis. Secure with the 5-40 setscrew. I use a little tape to keep the receiver wire from flopping around as well. Just be sure not to crimp the wire.
 Step 114 -
Feed the motor wires to the motor (through the shock tower) and solder into place. Remember, A wire to the A tab, B wire to the B tab and C wire to the C tab. Feed the sensor wire through as well and press into the motor.
 Step 115 -
Screw the 4-40 setscrews into the battery mount holes as shown.
 Step 116 -
Place the battery into the truck. Team Associated has supplied 4 foam pads (2 thick, 2 thin) so you can space the battery forward or back for better weight distribution. Since I’m not 100% sure how I want them to be yet, I placed them per the manual; 1 thick/1 thin up front, 1 thick/1 thin in the rear.
 Step 117 -
Slide the rear of the carbon fiber battery strap underneath the rear tower and drop into place (the holes in the strap should fit over the 4-40 setscrews). Secure the strap with the 2 Factory Team blue thumbscrews.
The Build – Part 7 - Body, Wheels and Tires
The final step in the Factory Team T4.2 build is the wheels, tires and body. For this step we’ll be using a full set of Proline’s Hole Shot T’s in their soft M3 compound. We will also be mounting the Proline’s Bulldog body painted up by none other than Larry over at Kustom RC Graphics.
Build Notes:
* We’ll be gluing up some tires, so I would suggest getting some tire-gluing bands and a good CA glue. I’ll be using Proline’s glue and LeadFinger Racing tire bands.
 Step 118 -
We start this tire-mounting process by first cleaning the tires to remove any oils or releasing agent left on the tires. We also cut a thin strip of the insert off to allow the tires to mesh better on the wheels. Turn the insert inside-out and cut a strip as shown. Not everyone does this, but I like to just because it makes mounting easier.
 Step 119 -
Fit the insert into the tire and wrap the tire around the wheels. Wrap your tire-gluing band around the tire and make sure the tire bead is pressed into the wheel channel. Using your glue (and a glue tip similar to CompetitionX’s Gloo Toobs), pull the tire back slighly and apply the glue. You’ll want to do all the tires on one side, then set them aside to dry (approximately 30 minutes for a good set). Flip the tires, move the tire-band to the other side of the tire and finish gluing the opposite side.
 Step 120 -
Once the glue has dried, you can mount the tires to the Factory Team T4.2 using the 8-32 wheel nut.
 Step 121 -
Don’t forget the wing shims…you’ll want to add these to help raise the rear of the body for a better fit. Note the orientation of the shims front-to-back.
 Step 122 -
Finally, drop your freshly painted body onto the body mounts and secure with the body clips.
And there you have it, a complete build of the Factory Team T4.2!
Page 1
Source:
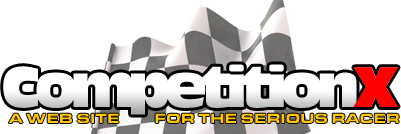
|