- Team Associated RC10 Classic - Tony Phalen - Build -
Page 2
The Build – Part 1 - Front Suspension
We start off the RC10 Classic build with the front suspension. If you’re a long time RC’er (or someone that just happened to have an original RC10 at one time), you’ll be happy to see all of the vintage-style parts in this kit. Let’s get started.
Build Notes:
* FIRST AND FOREMOST!!!! Do NOT throw away any of the tools AE has supplied. I’ll get to that more later, but if you decide not to use them, put them aside and, again, DO NOT THROW THEM AWAY!
* You’ll want to get your hands on a large-tip Phillips screwdriver for parts of this assembly. AE has included the old-skool aluminum Phillips screws and you don’t want to be stripping them out.
* Because this kit is from the way-back time-machine, the bags and their contents don’t coincide 100% with the manual. You may need to open bags further down the line to get the screws you need for an earlier step.
* Threadlock is also required during this assembly so have that ready as well.

The first step is to attach the front body mount to the front nose plate. Using one of the 8-32 (yellow) aluminum screws, feed it through the front nose plate, through a pair of #8 washers and into the front body mount. To make tightening easier, I installed a body clip to give the body mount more meat to hold on to.

Attach the front nose plate to the chassis using two more 8-32 (yellow) aluminum screws and the short 8/32 screw (silver). Feed the yellow screws in first (but do not tighten) followed by the silver one. A drop of threadlock on the silver screw will keep it in place. After you’ve snugged the silver screw down, snug the yellow ones down.

Assemble the steering rack arms as shown. The plastic on these is very similar to the original plastic from years ago, so be careful when tightening down the ball ends. SNUG them down…do not overtighten.

Slide a #8 washer over both yellow screws in the chassis followed by the assembled steering rack arms. Note which arm goes on which side. Slide the servo saver arm onto the LEFT side servo arm as shown and secure both steering rack arms with a 8-32 white nut. Tighten down until snug, then back off about 1/2 turn. You’ll want the steering rack arms to move freely but with as little slip as possible. Adjust the white nuts until you achieve this.

Install a ball end into both caster blocks. Note the orientation of the caster block.

Assemble the steering blocks as shown. You’ll want to make a left and right side. A drop of threadlock will keep the nut attached to the ball end.

Align the hex on the axle with the hex on the steering block and slide it into place. It may take a little pressure to make it seat all the way into the steering block. Secure with an e-clip.

There are three different sizes of hinge pins included in this step. The one of the far left is the kingpin, the one in the middle is the outer hinge pin and the one on the right is the inner hingepin. Grab the one on the left…

…attach an e-clip to one end and slide it through the caster block and steering block as shown. Note the orientation of the parts. Secure the kinpin on the bottom with another e-clip. Make both sides.

The suspension arms will require a bit of ‘massaging’ to make them move freely after assembled, so this is a good time to do it. Take your hinge pins and slide them through the arms…they should take quite a bit of pressure to push through and the arm will most likely not ‘swing’ on it. We’ll need to remedy that before we move on. Take a 1/8? drill bit, attach it to your dremel or drill and, on a slow speed, ream out the inner and outer holes of your suspension arms. Test the hinge pin again. If the arms swings freely, you’re good to go. If not, repeat the reaming process until it does. Do this to both the inside and outside hinge pin holes on both arms.

Using the ‘middle’ hinge pin (as described earlier), snap an e-clip to one end and attach the caster block/steering block assembly to the front suspension arm. Note the orientation. Secure with another e-clip on the other end of the hinge pin. Build both sides.

The next step is the shock tower. As you can see, old-skool shock towers were flat so there isn’t a front or back side…just a tower. Start by attaching the shock mount screws to the single hole in the top. The shock mount screws will be in a later bag so you’ll have to find them. Don’t forget the #4 washer and the drop of threadlock to keep the 4-40 nuts in place.

Slide the ballstuds into place and secure with a 4-40 nut. A drop of threadlock here is also required.

Attach the shock tower assembly to the left and right arm mounts as shown. Note the orientation of the arm mounts. When you’re done, press the assembly on a flat surface (as shown) and rotate the arm mounts until they are flat against the ground.

Now attach the shock tower/arm mount assembly to the chassis using 6 of the 8-32 (yellow) screws. Slowly tighten each one to make sure you don’t tweak the final setting point.

Snap an e-clip to one end of the longest e-clip and attach the left and right suspension arm assembly to the arm mounts. Secure with a final e-clip. I found that sliding the hinge pin up from the bottom (as shown) made snapping the 2nd e-clip on much easier.
The Build – Part 2 - Transmission
In Part 2 of the RC10 Classic build, we jump into building an excellent rendition of the original 6-gear transmission. This transmission is simply over-complicated by todays standards and, because of this, the transmission build is a bit longer than most steps. It is a cool look at how things were done back then though!
Build Notes:
* In Step 1 I tried to make it extremely clear not to throw away any of the tools AE supplied with the RC10 Classic…and now you’ll find out why. In Step 7 you’ll need to screw in some itty, bitty 0-80 size screws into the RC10 idler gears. Ya, well, unless you’ve got an over-abundance of useless tools, you won’t have the L-wrench needed for this step. AE does supply it but, if you’re like me, I tossed out all those cheezy tools in favor of my awesome Hudy and MIP ones. Problem is, Hudy and MIP (or any other tool manufacturer in our industry) doesn’t make a 0-80 size wrench! So, yah, I had to order another 0-80 size wrench from AE. Moral of the story: don’t throw your RC10 Classic tools out. Ever.
* Have some threadlock ready as you’ll need it for this step.
* Because this kit is from the way-back time-machine, the bags and their contents don’t coincide 100% with the manual. You may need to open bags further down the line to get the screws you need for an earlier step.
* You’ll also be dealing with alot of grease, so a couple clean towels are recommended.

We start off the transmission build by pressing the drive pin through the drive gear pivot. This fit is a bit tight and might give you a bit of grief installing, but once you get it started just make sure it’s centered in the drive gear pivot.

Slide the drive gear pivot assembly through the spine plate as shown and secure with the drive gear pivot nut. Note the orientation of the spine plate. Don’t forget to add a drop of threadlock to the drive gear pivot nut.

Slide the idler gear pivot through the spine plate, attach the 5mm washer and snap the larger e-clip into place as shown. Make sure you use the bowed e-clip and note the instructions on which side of the ‘bow’ faces out.

Press an oilite bushing into each of the axle drive gears. Make sure it seats all the way down into the gear and secure with an internal retaining clip (or snap ring). If you have a set of snap ring pliers, you can use those here to make things a bit easier. If you don’t, you can force one of the ‘open’ ends in and, carefully using your fingernail, rotate the snap ring into place.

This photos shows the snap ring fully seated. Make sure both of your gears look like this.

Slide the assembled axle drive gears onto the drive gear pivot as shown and secure with the 4-40 screw. A dab of threadlock will help keep the screws from loosening up.

Press the oilite bushings into the idler gear and secure with 4 0-80 screws. You did save that itty, bitty 0-80 L-wrench, right? If you didn’t, you’re SOL until you fine another…don’t try and force the screws into place with a different wrench.

Slide the idler gears onto the idler gear pivot and secure with an e-clip. Note the orientation of the gear…you’ll want the screw heads facing out.

Before we assemble the top shaft, we need to do a little pre-prepping of parts. Trust me, it’s makes it alot easier! Start by pressing the white diff bushing into the thrust washer with the larger hole. Press in until one side is flush. You can use your table to achieve this (as shown in the photo).

Press one of the larger oilite bushings into the bearing adapter. Make sure it is seated completely.

Finally, press the 2nd white diff bushing into the diff hub as shown. Make sure it is flush with the outside.

Now that the prepping is done, time to assemble. Slide the diff washer (with the smaller hole) onto the top shaft followed by the diff thrust bearing. Apply a small amount of black grease onto the ‘gear-side’ of the thrust bearing and slide down to the diff washer.

Apply a little more black grease onto the opposite side of the thrust bearing. Take your diff washer/diff bushing assembly and slide it onto the top shaft, the ‘flush’ side facing the thrust bearing. Slide it down and into place.

Slide the diff pinion onto the top shaft followed by your bearing adapter assembly. The diff pinion should slide over the white diff bushing and the bearing adapter should slide over the flange on the diff pinion.

Take your diff tube assembly and slide it onto the top shaft (tube-side first) and press the entire assembly together.

For the next couple of build steps, it’s easier if the top shaft is facing up. I used the transmission case half to hold the top shaft in place. Once you’re ready, slide a diff ring into place on the diff hub.

Slide the spur gear into place (over the diff hub) and squeeze a drop of white lube into all 8 holes as shown.

Drop one diff ball into each of the 8 holes. Be careful as these little suckers like to roll away and can easily be lost in the carpet.

Prep the diff spring by compressing it 2-3 times with a pair of pliers.

Drop the 2nd diff ring into place followed by the outer hub. Make sure the diff ring seats around the flange on the hub.

Drop the diff spring in place and attach the 5-40 locknut on the end. You can start with AE’s recommendation of tightening the locknut down until it is flush with the top shaft.

Ok, are you still with me? Well now we’re on to the fun part… Take your spine plate assembly and insert it into the right transmission case. Note the orientation of the spine plate in the picture.

Slide the top shaft through the aluminum motor guard and through the upper hole in the right side transmission case. You’ll also want to make sure that the bearing adapter (on the top shaft) mates correctly on the outside of the transmission case.

To help with the following step, cut a small notch in the final bearing adapter as shown. It doesn’t need to be a big notch, just something you can get a set of needlenose pliers into. Press the final oilite bushing into the bearing adapter.

Press the bearing adapter into the left transmission case half. Using all three of your hands, align and press the two transmission cases halves together.

Drop the e-clip into the bearing area and, using the notch you cut earlier, snap it into place.

Press a felt ring over both of the diff outdrive gears followed by the felt seal. A drop of CA glue (on each ‘tab’) will help keep the felt seal in place. It should only take about 10 seconds to cure.

Insert the 4-40 plain nut down inside the hole as shown…

…and secure the transmission together with the 4-40×5/8 screw. Do not over tighten, but do apply a small drop of threadlock. Now insert the 3 longer 4-40 screws and tighten them to the aluminum guard. A small dab of threadlock on these is also recommended.

The final assembly should look like this and the gears should spin somewhat freely. Time to take a breather and get a beer. Good job.
The Build – Part 3 - Rear Bulkhead
The next assembly step involves attaching the rear bulkhead, shock tower and transmission to the chassis. Pretty straightforward with no surprises.
Build Notes:
* Have some threadlock ready as you’ll need it for this step.

We start off by assembling the rear shock tower. Insert the two 4-40 screws through the tower and secure with the 4-40 nuts. The shock tower is not directional so it doesn’t matter which side you start with. Threadlock is recommended here to make sure the screws don’t loosen up.

Attach the assembled shock tower to the rear bulkhead as shown. Note the orientation of the top screws.

Flip the assembled rear bulkhead around and insert two of the silver ballends. I used the holes per the instructions, or the inner-upper holes. Do not overtighten these screws.

Wedge the bulkhead between the two tabs on the rear of the chassis and secure the bulkhead with two of the 8-32 yellow screws.

Insert and tighten two of the 4-40 screws into the side of the chassis tabs as shown.

Place the transmission into place and secure it to the chassis with 4 of the 8-32 yellow screws.

Attach the rear body mount to the transmission brace. As with the front body mount, I inserted a body clip to make holding onto the body mount much easier.

Thread the two 4-40 screws into the back of the motor guard and into the motor plate. Use threadlock to prevent them from backing out.

Attach the transmission brace as shown. Be sure the rear body mount is set to the front of the assembly. Do not overtighten these screws.

Insert the wing tubes into the holes as shown. This will take a little bit of pressure to do, so it is suggested that you place something soft over the top of the tubes and GENTLY tap into place with a hammer. The instructions say to use a dab of CA to keep them in place, but I would only suggest that if yours slide into the holes easily.
The Build – Part 4 - Rear Suspension & Turnbuckles
In Part 4 of the RC10 Classic build, we attach the rear suspension and assemble the turnbuckles.
Build Notes:
* Unlike current cars, the roll pins that feed through the rear axles are just that, rolled steel pins. They’re a pain in the butt to install and it is easy to pinch your fingers, so extreme care is suggested during this step.
* The turnbuckles are also old skool…threaded rod with ball cups on each end. Care must be taken here as well to not damage the threads during assembly.

We’ll start off this step with getting our hinge pins in order. There are 2 sizes; a short and a long. The short is your outer hinge pin, used out on the hub carrier. The longer one is your inner hinge pin, used to connect the suspension arm to the arm mount. Let’s grab the two long ones and attach an e-clip to one side.

Slide the hinge pin through the arm/arm mount combo. The arms and mounts are directional so make sure you have the left arm mount with the left suspension arm and the right arm mount with the right suspension arm. Once assembled, secure the hinge pin with another e-clip.

Attach both arm mount assemblies (right assembly to the right side, left assembly to the left side) to the chassis, as shown, using the forward set of holes.

Press the four oilite bearings into the hub carriers as shown. Make sure they seat completely flat.

Slide one of the 1/4 axle shims onto the axle, then slide that assembly through the hub carrier. Finish that off with 2 more 1/4 axle shims.

Here is the tricky part. The roll pin is going to be a slight bit bigger than the hole it needs to go into. To make installation easier, crimp one edge of the roll pin slightly, making this end slightly smaller in diameter than the rest of the pin.

Press the roll pin into the hole in the axle with the smaller edge. Make sure you force the smaller edge you created in step 62 into the hole first. Center the pin in the axle as shown. This will require a little bit of patience.

Test fit the hub assembly into the rear wheel, making sure the roll pin completely fits in the groove. If not, try centering the pin again.

Here is a picture of both of the assembled hub carriers.

Grab the shorter hinge pin and attach an e-clip to one end. Now attach the hub carries to the rear suspension arms as shown and secure with another e-clip. Note the direction of the hub carrier, keeping the ball end facing towards the front of the car.

The turnbuckles on the RC10 Classic consiste of 3 lengths of threaded rod. The shortest one connects the steering bellcranks, the 4 mid-length ones are for the camber links and the 2 longest ones are for the steering.

Grab a pair of the mid-length rods and build a pair of links as shown. Use the manual-supplied gap of 14.2mm. A pair of gloves or a spare rag will help keep the ballcups from cutting into your hands as you build.

Insert the dogbone springs into the rear axles as shown.

Pop one end of the turnbuckle onto the inner ball stud. Insert the dogbone into the transmission outdrive, swing up the rear outdrive and key the dogbone into the rear axle. Finish this assembly by popping the ballcup onto the ball stud on the rear hub. Do this with both sides of the car.

Grab the shortest-length threaded rod and build the drag link. The manual-supplied gap of 12.44mm is a good start.

Pop the drag link onto the inner ball studs of the bellcrank as shown.

Grab the final pair of mid-length threaded rod and build a pair of front camber links. Use the manual-supplied gap of 13.5mm.

Pop the camber links onto the camber ball studs as shown.

Grab the longest pair of threaded rod and build two steering links. The gap of 27.7mm is a good place to start.

Pop the steering links into place as shown.
Page 2
Source:
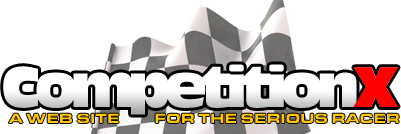
|