- Team Associated B6D - Joel Navarro - Build -
Associated blind-sided us with rumors first of a new buggy, then teased us with a 3D printed mock up that everyone thought was just a B5m with a laydown transmission with finally announcing the B6 and B6D…the most wanted kit right now. Well now we have our hands on both B6 and B6D! Follow this post and see the step by step process of putting together this world class car.
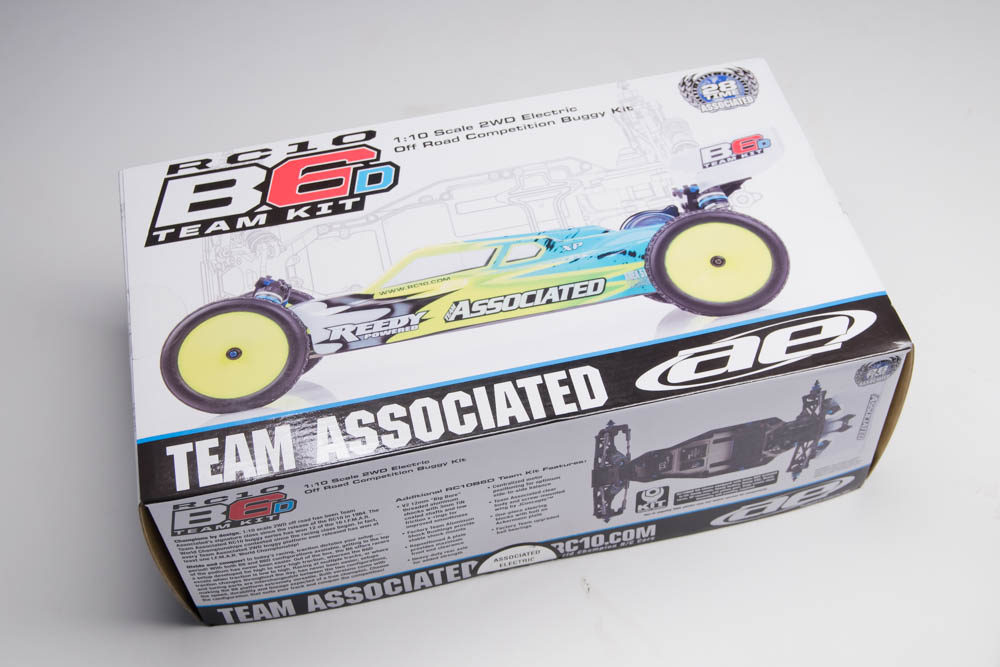
Pictured is the B6D (D for Dirt) instruction manual. Both the B6 and B6D will be almost identical builds with the exception of the B6 having a laydown transmission, gullwing front suspension arms and different front shock tower.
|
|
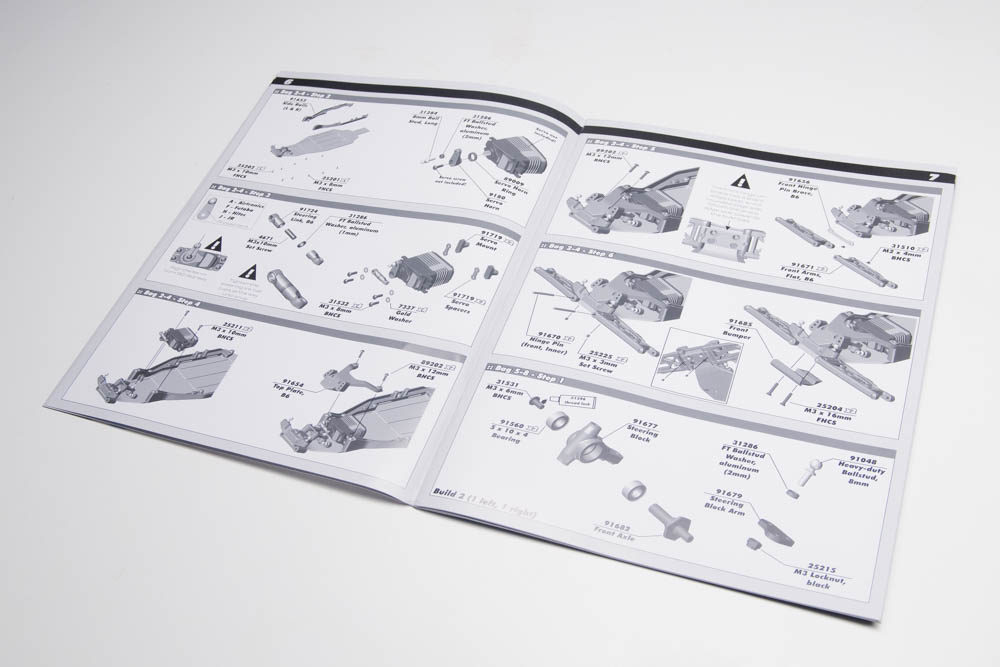
|
|
This is the view when you first open the kit box. All parts are bagged and labeled and later opened with a corresponding step in the manual.
|
The Chassis
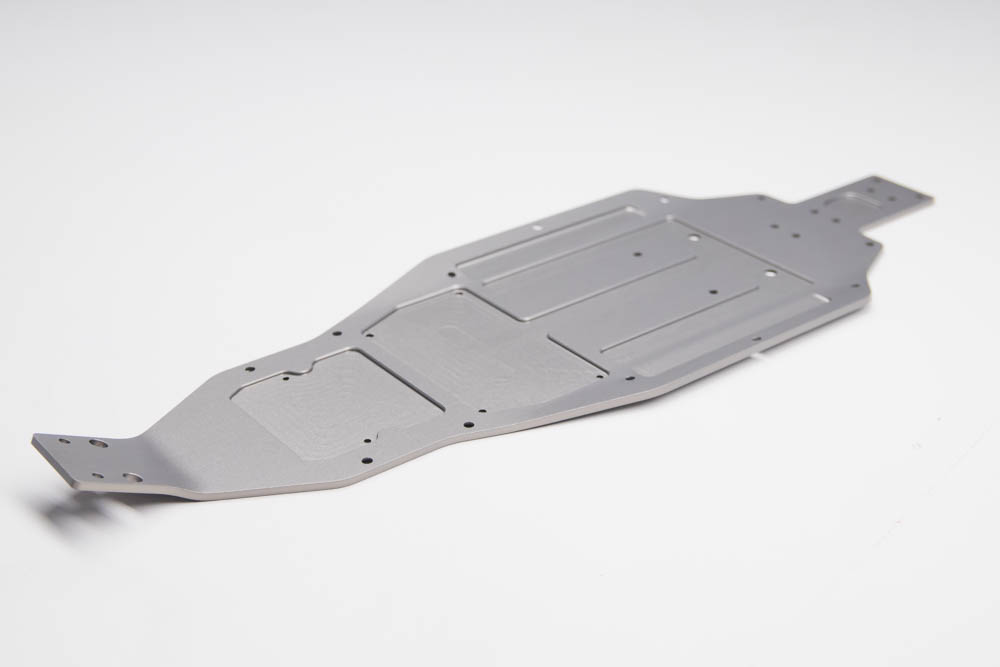
Both cars will use the same 2.5mm chassis. It is drilled to accept both stand up and laydown chassis. Front kick is now built in to add strength and consistency to the front-end parts and suspension. On the scale, the new chassis weights 134 grams versus the B5m Lite chassis weighing 107 grams.
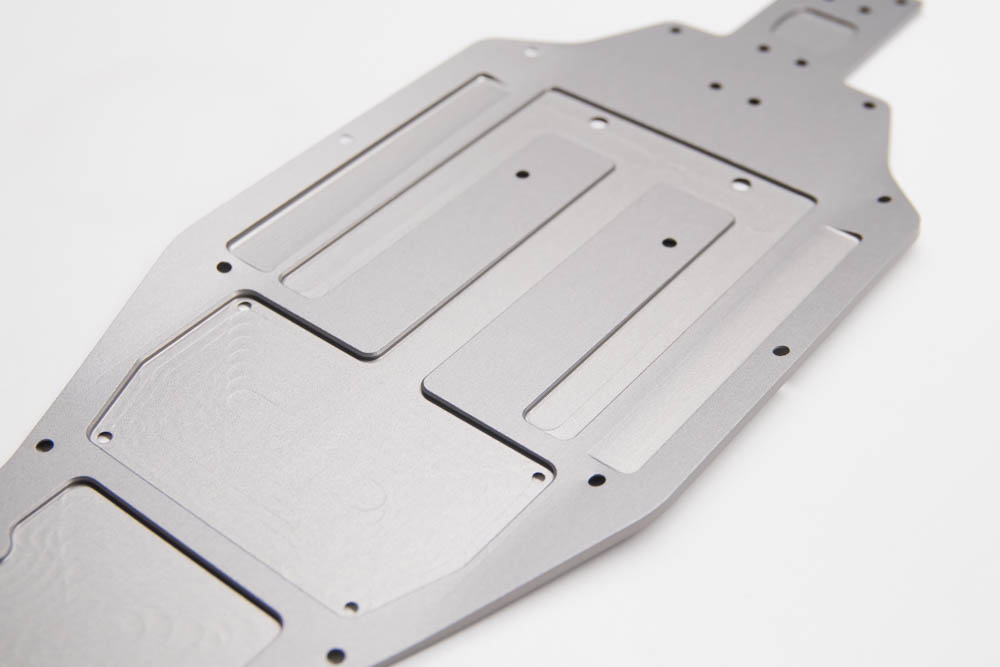
The chassis is milled for lightness and to add some flex. The areas under the servo and where the speed control will mount have small holes drilled in them to screw on steel or brass plate to add weight when needed or to change the bias. Or you can use the steel plate under the speed control area to quickly unscrew it if you want to clean or maintain the B6 versus undoing double sided tape.
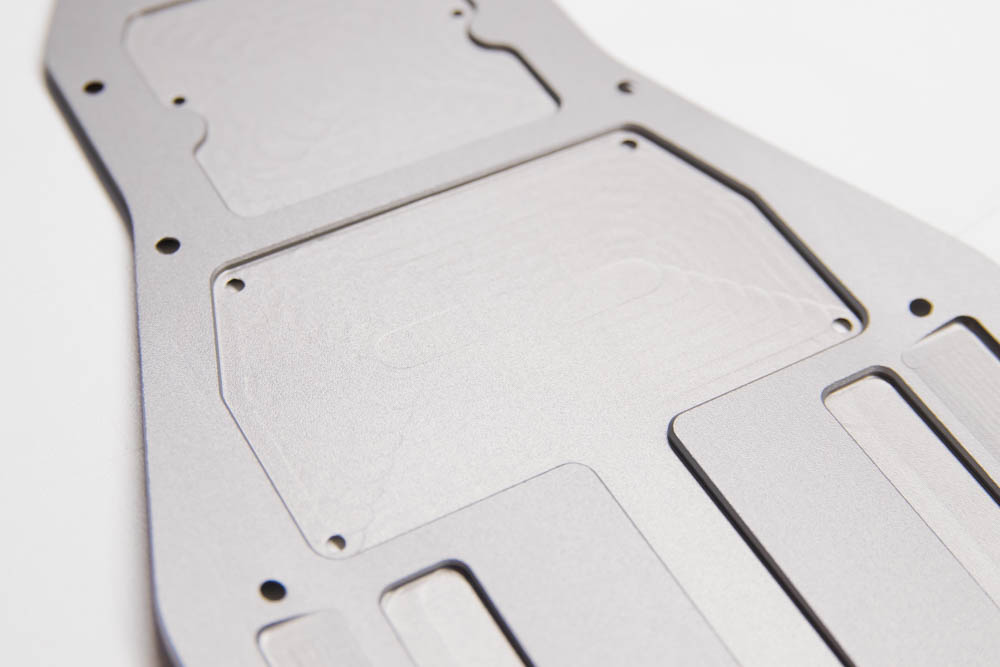
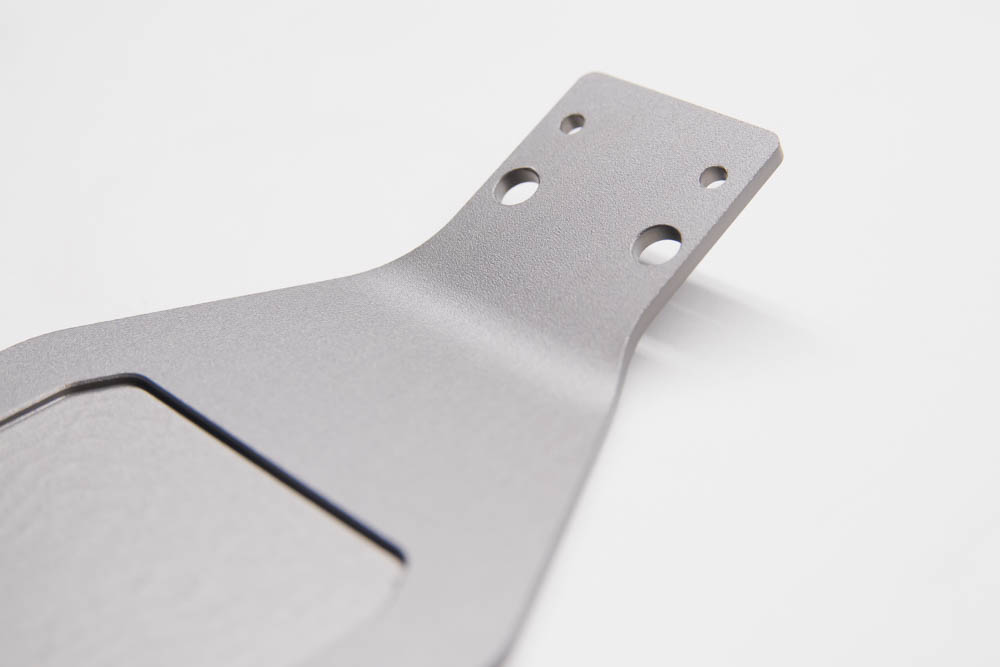 Front kick-up is now built into the chassis to beef up the front end.
|
|
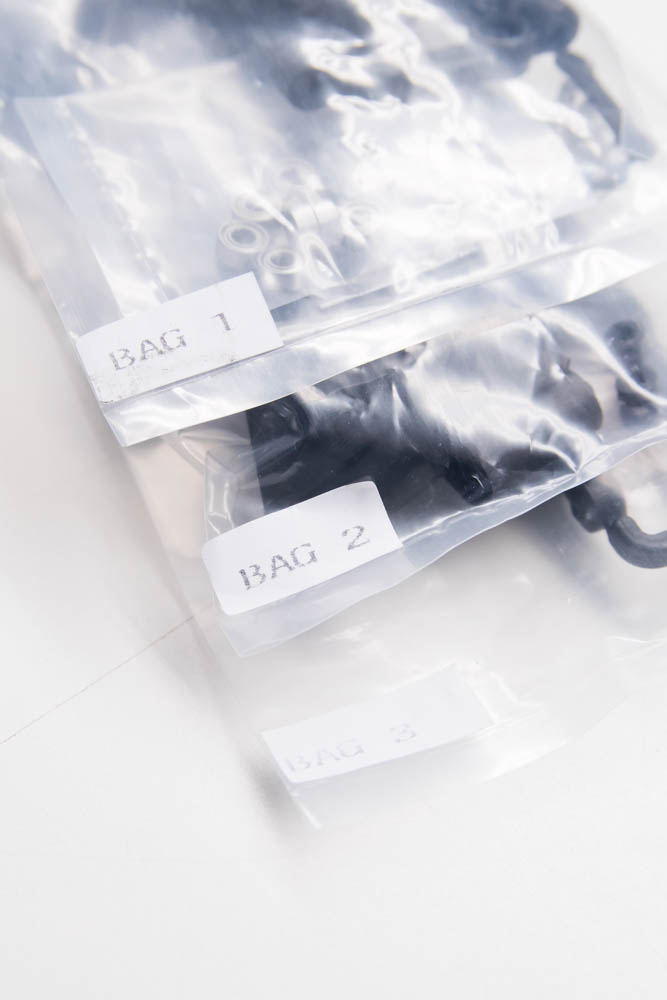 Right before I start the build, I organize the clearly labeled parts bag by standing them up in numerical order in the kit’s box.
|
Front End
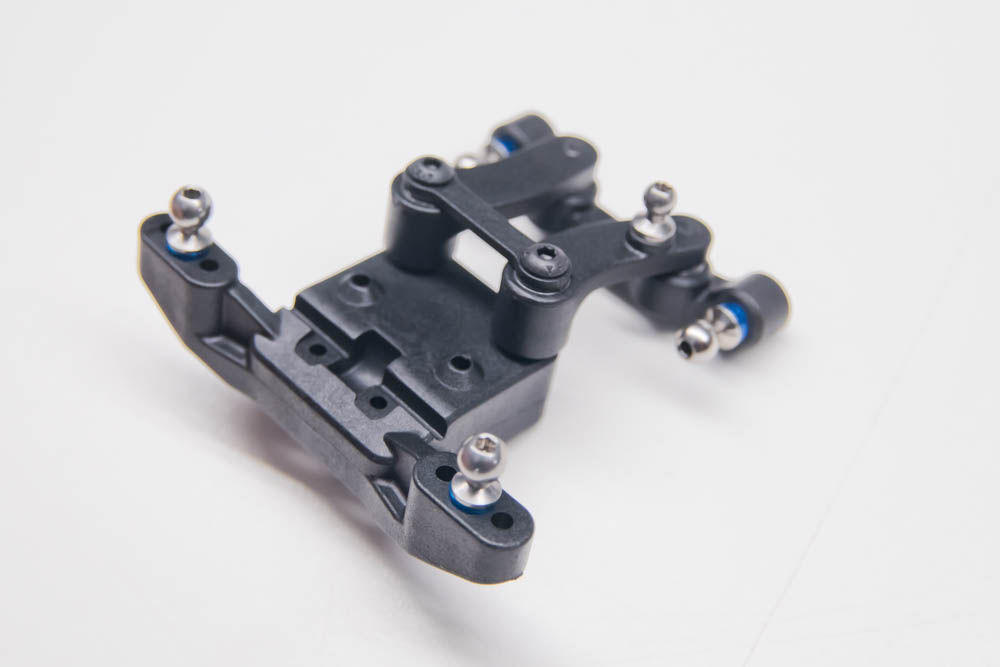
The build starts off with assembling the bellcrank steering and front ball stud mount. The steering parts rides on ball bearings for ultra smooth operation and precision. The manual has you install a 2mm blue aluminum washer under steering ball stud to set the ackerman. A 1mm blue aluminum washer is installed under the camber link ball stud.
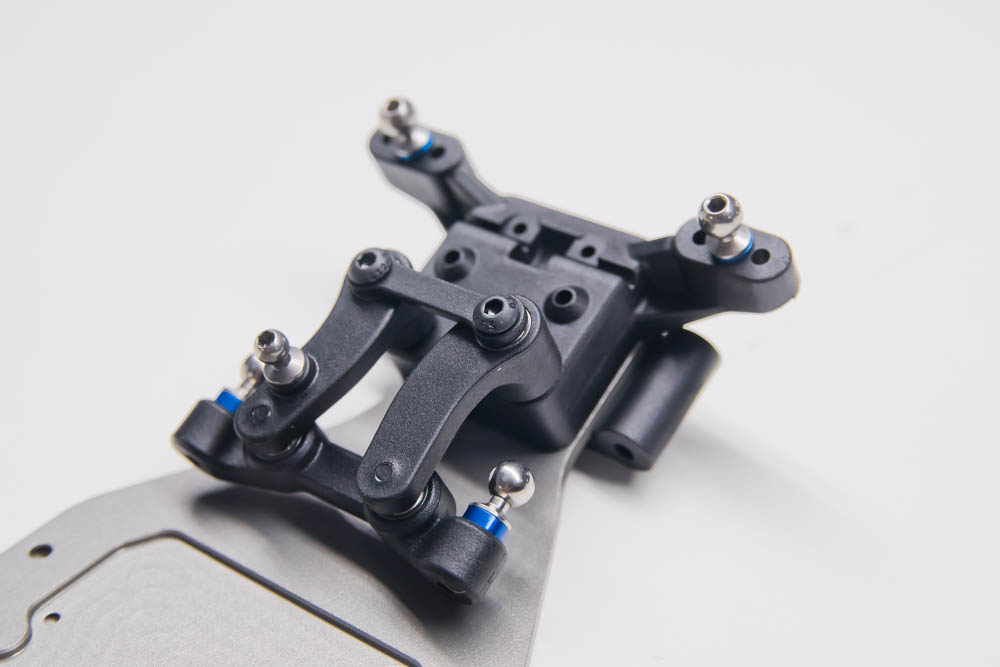
Once the steering is ready to mount, the front bulkhead will mount with it. With two settings built into the bulkhead (25 or 30 degrees), the stock setting is 25-degrees.
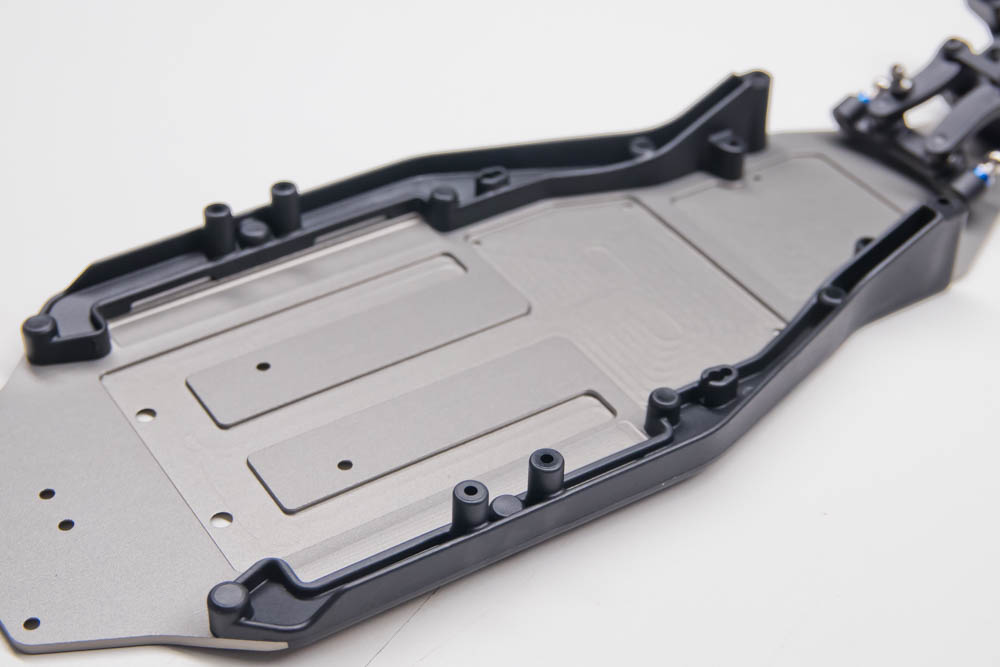
The side rails go on next attaching with six 3x8mm and four 3x10mm countersunk screws. The side rails should be a great tuning aid to alter chassis flex by either loosening screws a half turn or omitting some.
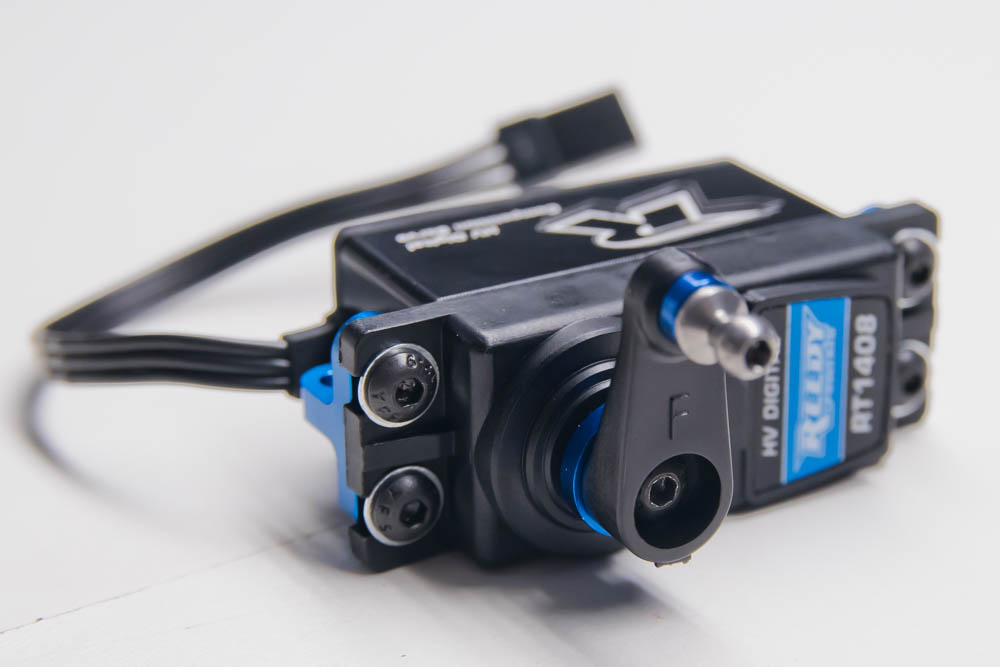
The manual next has you prep the steering servo for mounting. The B5 blue aluminum servo mounts and servo horn are the only parts so far carried over to the B6/B6D. I used the thicker servo spacer to scoot the servo more forward on the car.
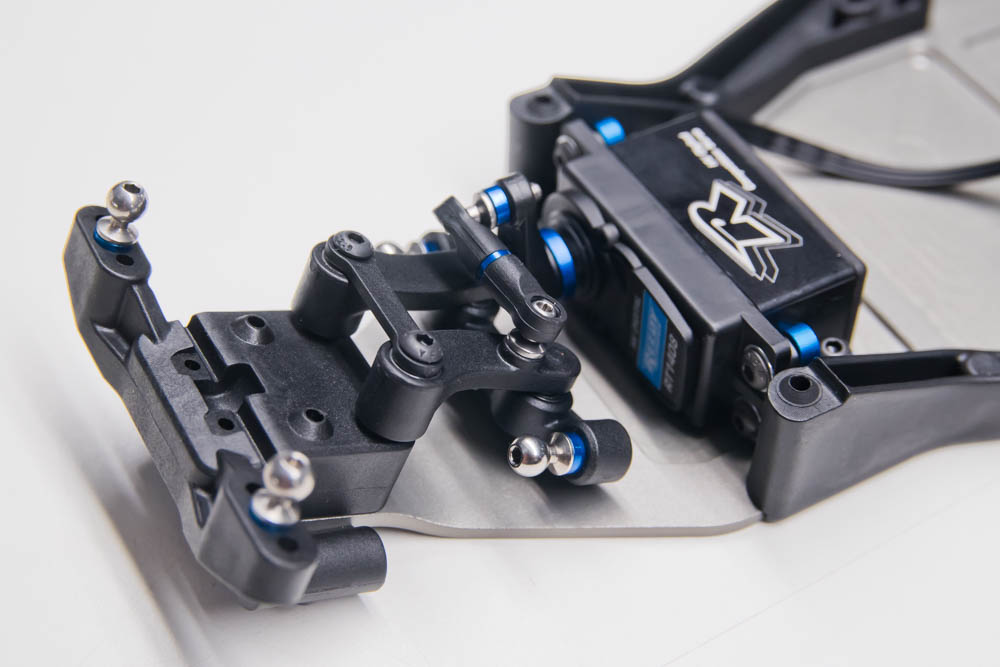
The servo mounts to the chassis with two 3×10 button head screws. The servo link uses a 1mm blue aluminum washer in between the plastic ball cups to take any guess work out of the over all length.
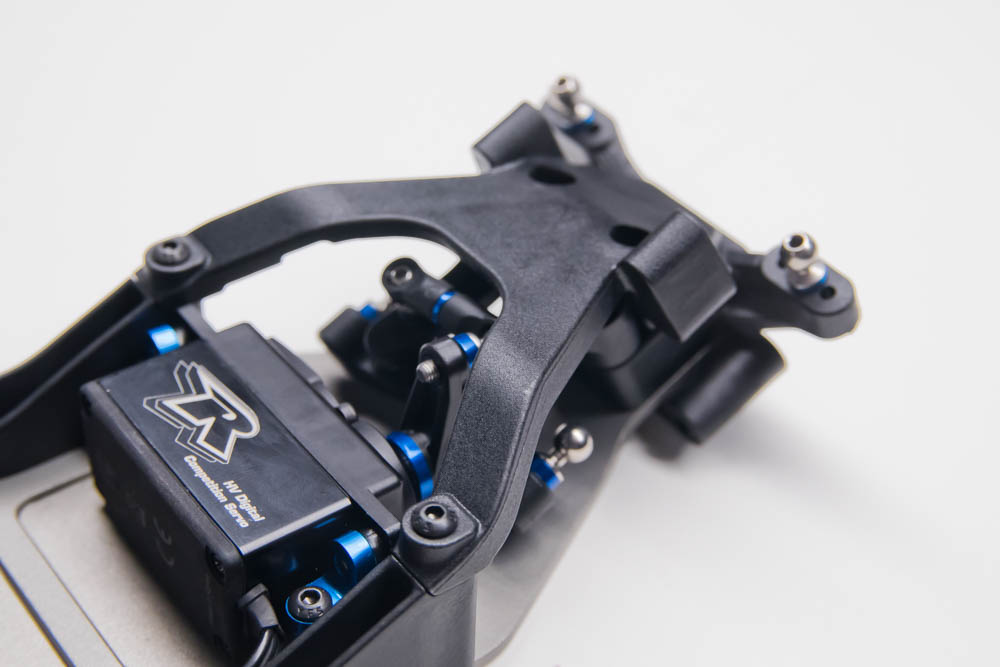
The top plate finishes the front end of the chassis attaching to the side rails and ball stud mount. Incorporated into the top plate is the front shock tower mount.
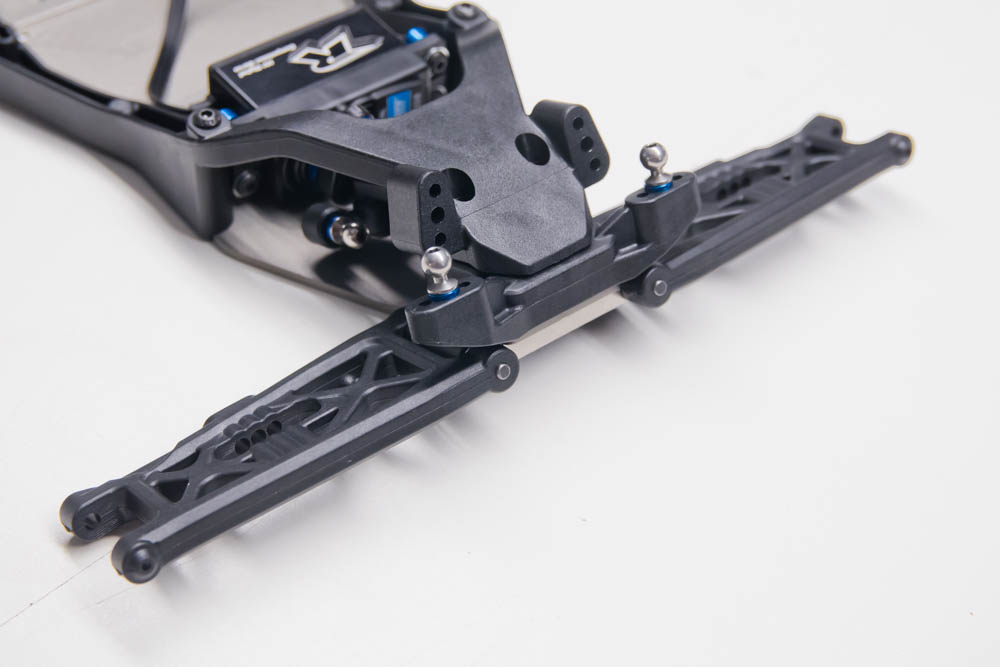
The front arms mount differently from how the B5m did. The hinge pins insert the same way and a small screw on the trailing end holds them in. A set screw in the bulkhead now holds them in place instead of the blue aluminum front hinge pin brace.
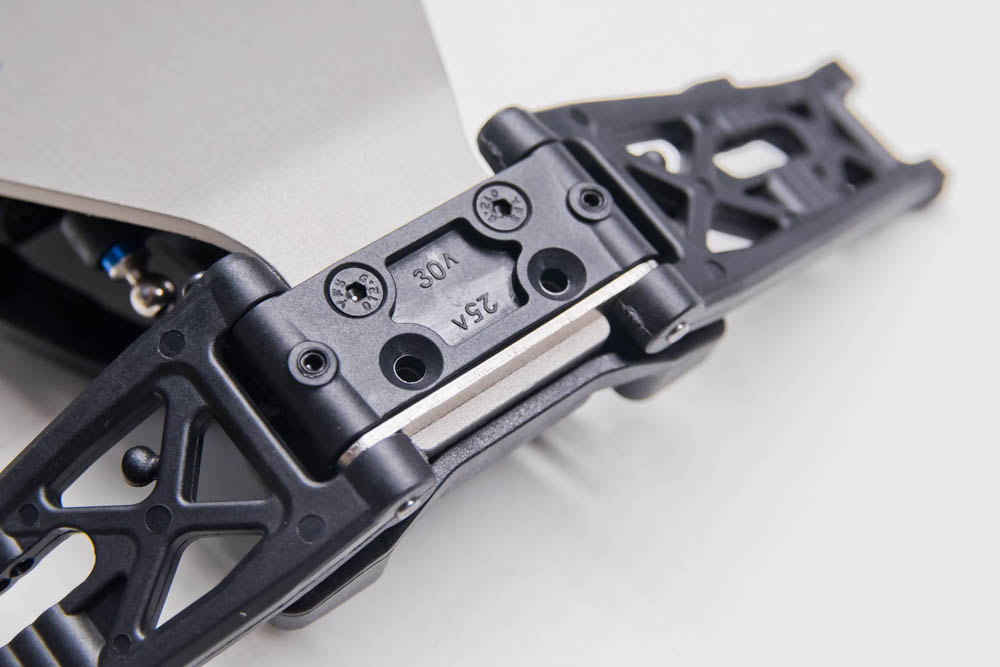
The setscrew in the plastic bulkhead keeps the hinge pins from sliding out. Note the metal hinge pin brace sandwiched between the bulkhead and behind the leading edge of the arm.
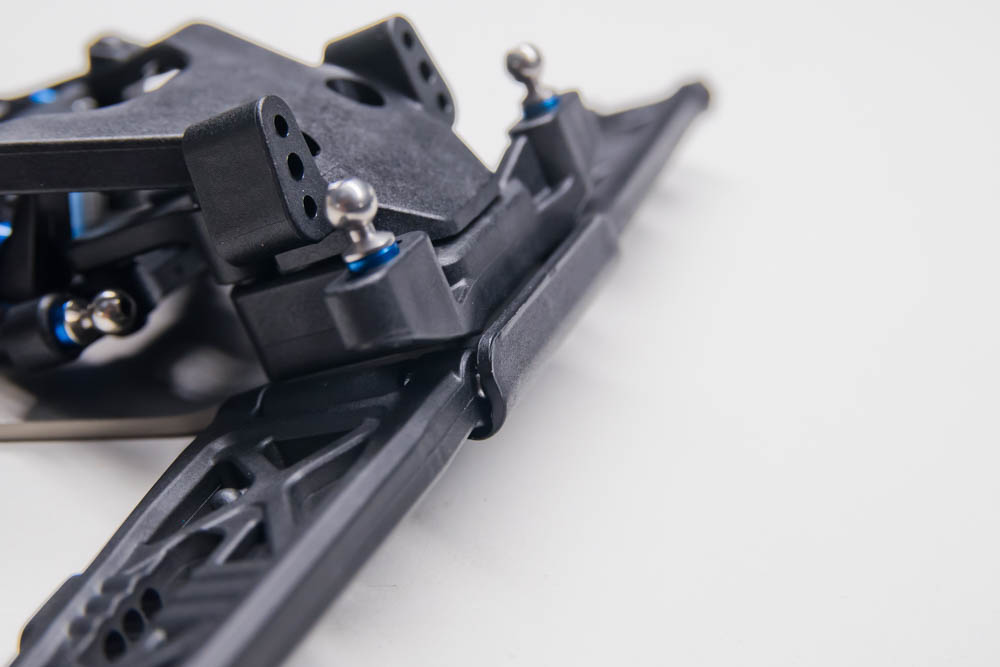
The front bumper attaches on last, adding protection and further holding in the suspension arm hinge pins.
|
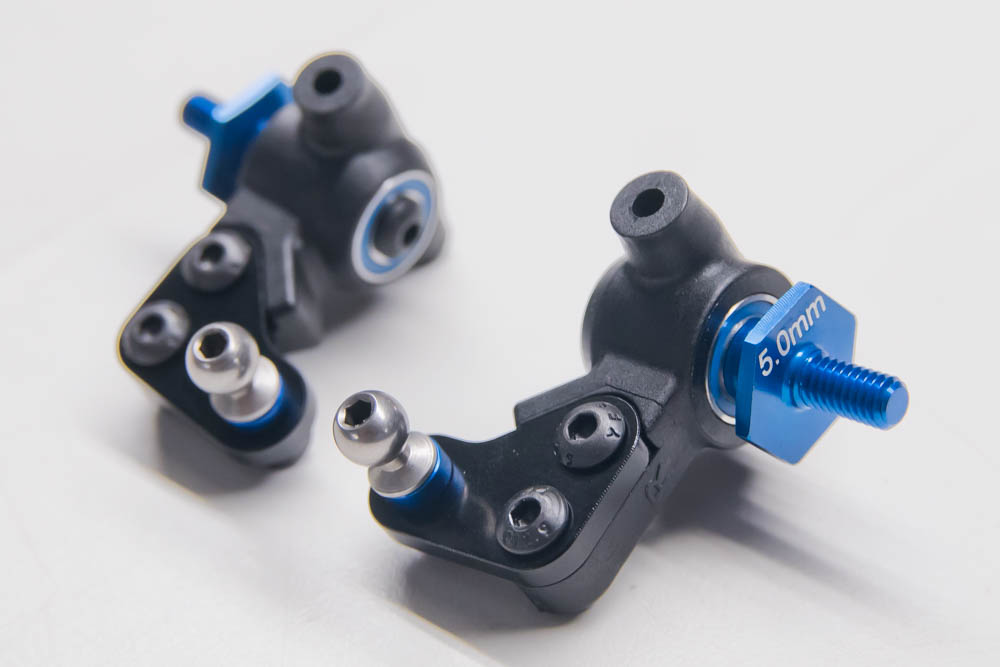
The steering blocks are next to be prepped and mounted in the front caster block. The bearings go in on either side (without a crush tube like the B5m did) followed by inserting the aluminum 5mm offset front axle. The metal steering blocks are attached to the steering block via two screws. The ball stud has a 2mm blue aluminum washer underneath and held in with a 3mm nut.
Setting the caster angle on the caster block is as easy as putting in a plastic insert. With the tab up on the #5 insert, as pictured, sets the overall caster at 30-degrees versus tab down 20-degrees if the tab was down.
|
|
The kit comes with three total caster block inserts to choose for a multitude of adjustment.
|
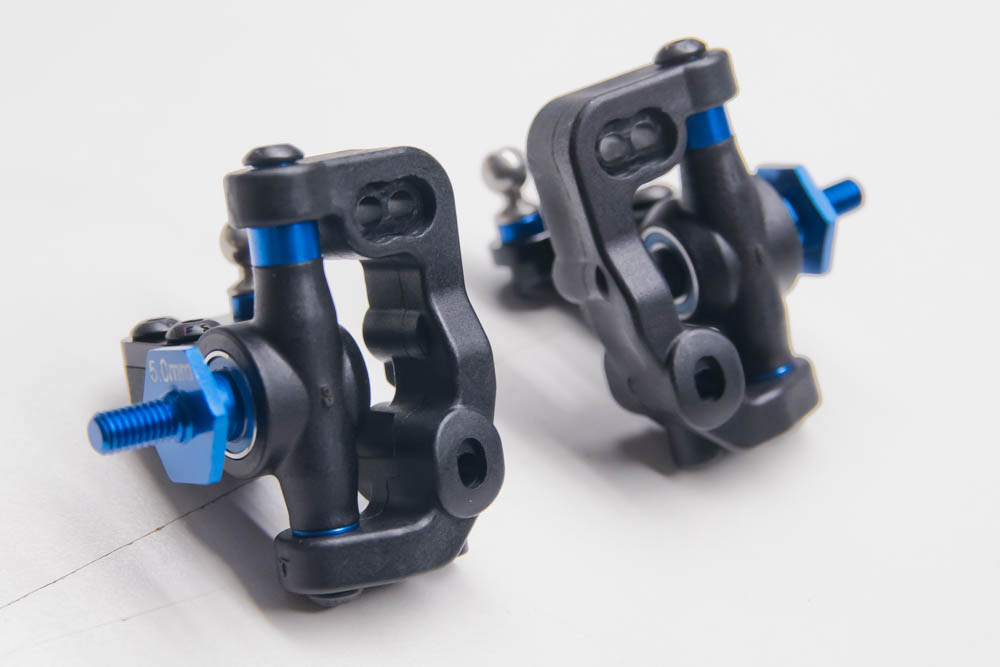
Here are both steering blocks finished and ready to mount to the car. Note the height adjustable steering blocks. Swapping the blue aluminum steering bushings change the axle height.
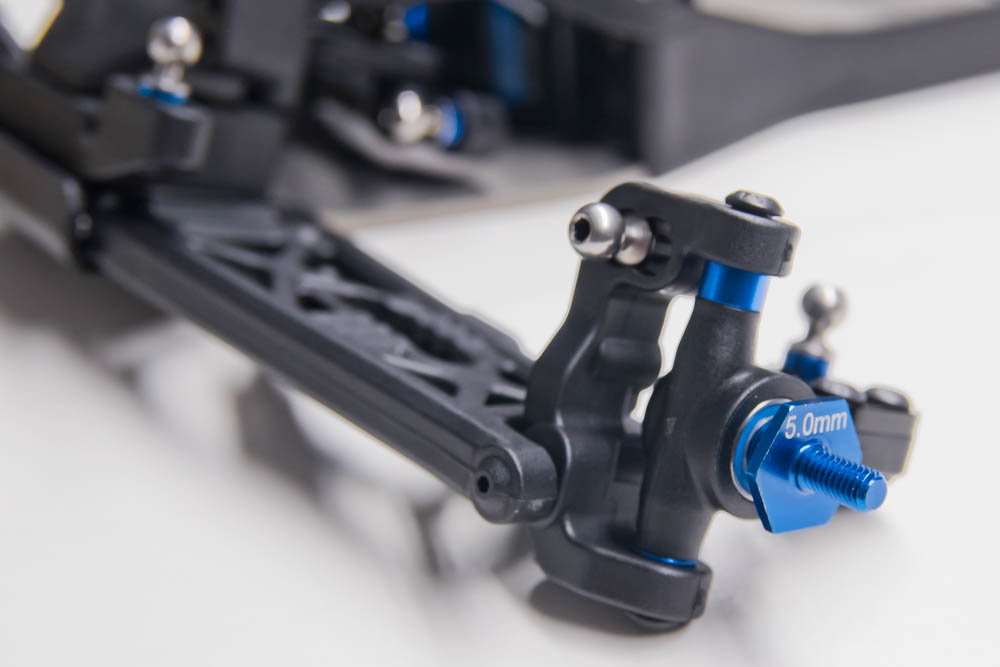
Once mounted on the suspension arm, the ball stud is added and ready to accept the camber link.
Rear End
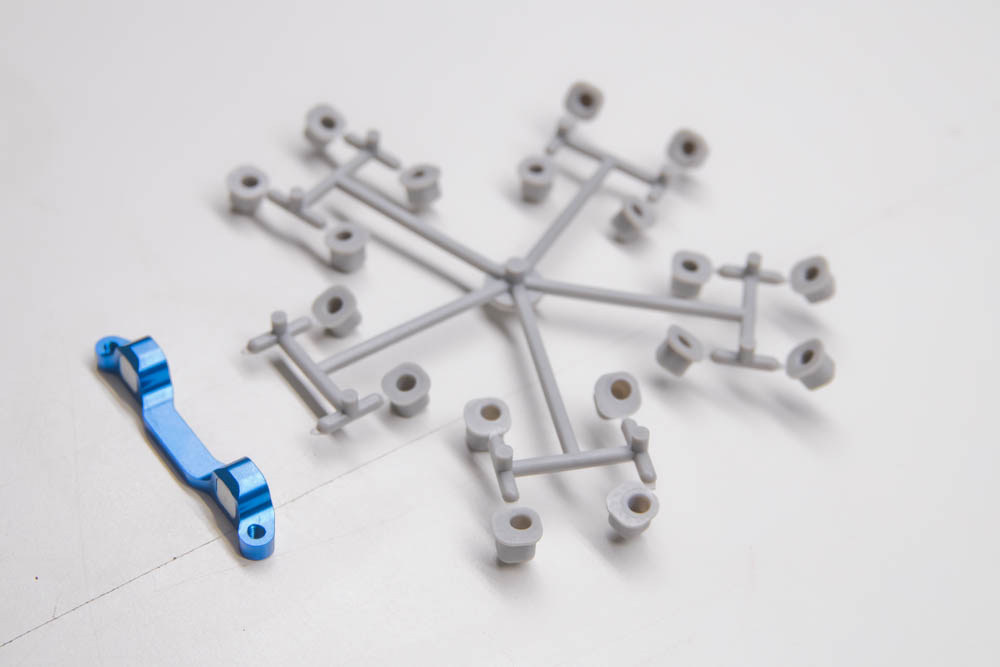
Moving to the rear end, the blue aluminum C-block arm mount is next to be installed. The B6/B6D is supplied with a various plastic pills that allow you to change the rear toe and anti squat in the rear arms. The stock setting is the pill with the hinge pin hole directly in the middle.
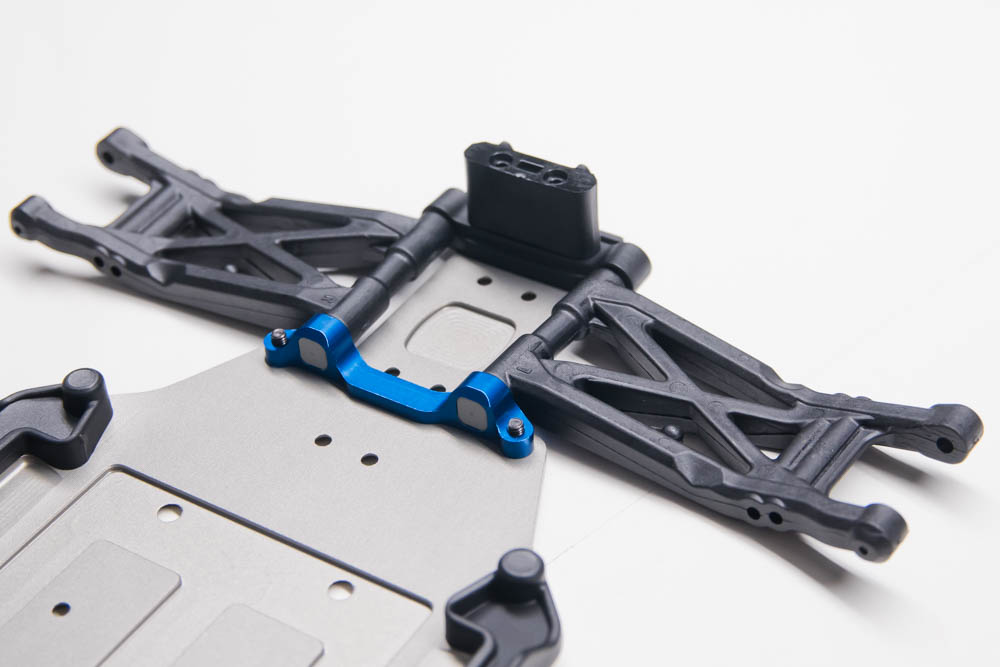
Using the C-mount and the plastic D-mount, the rear arms mount the chassis. A rear anti-roll bar mount sits atop the D-mount. There is an aluminum D-mount available that accepts the same pills as the C-mount that allows further adjustment.
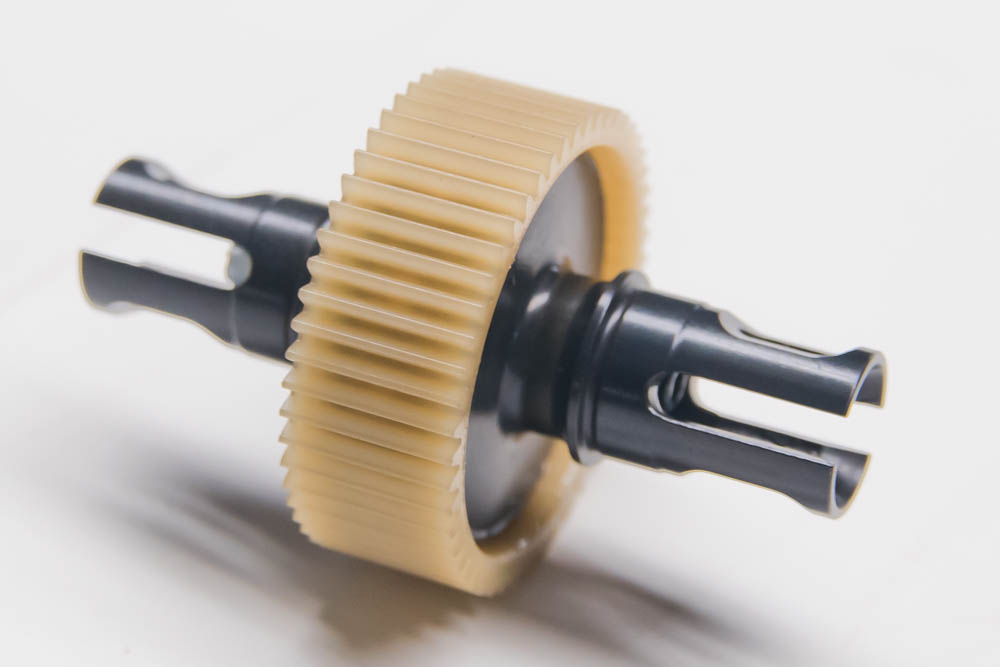
The B6 comes with a gear diff and the B6D a ball. The ball diff in the B6D is a pretty standard diff balls and thrust bearings unit that spins internally on bearings. New features to B6D differ are milled out lightened steel outdrives.
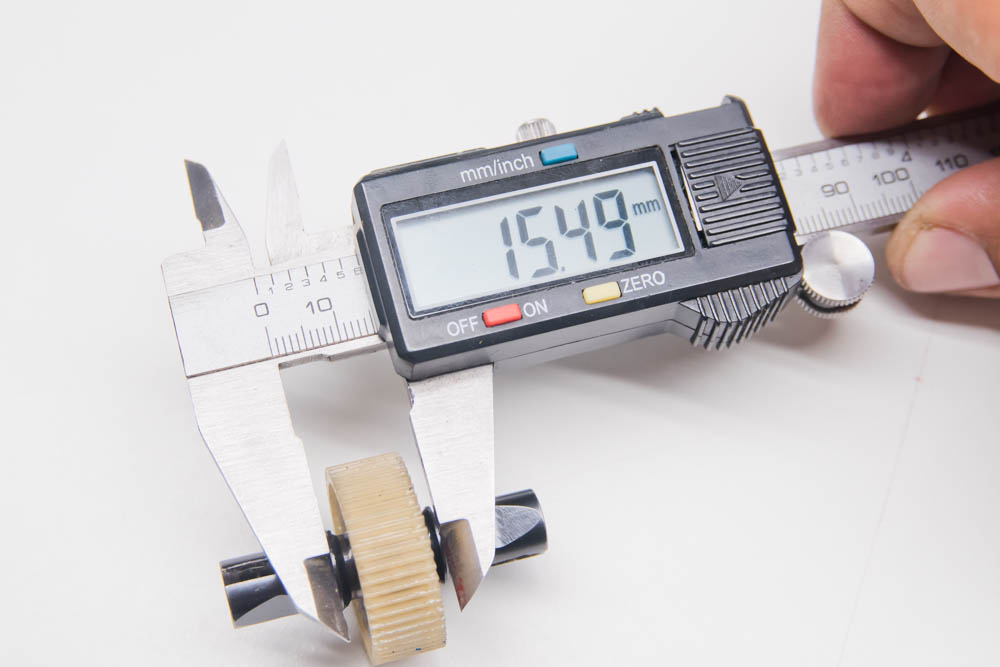
The new ball diff is slightly wider. The new diff measures approx. 17.6mm while the B5 diff measures approx. 15.5mm. If you race stock and want to transfer your MIP Puck system over to the B6, you will have to use washers on the outdrives for proper spacing.
|
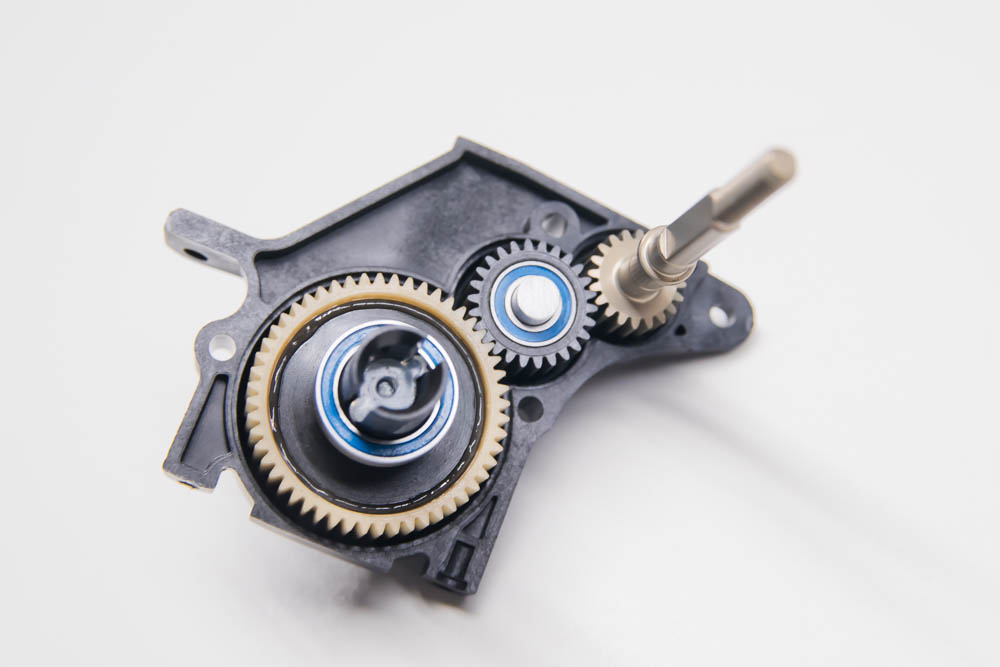
This is what the B6D tranny looks like right before you close it up. The laydown transmission can use the same diff and top gear, but you will have to get the larger idler gear.
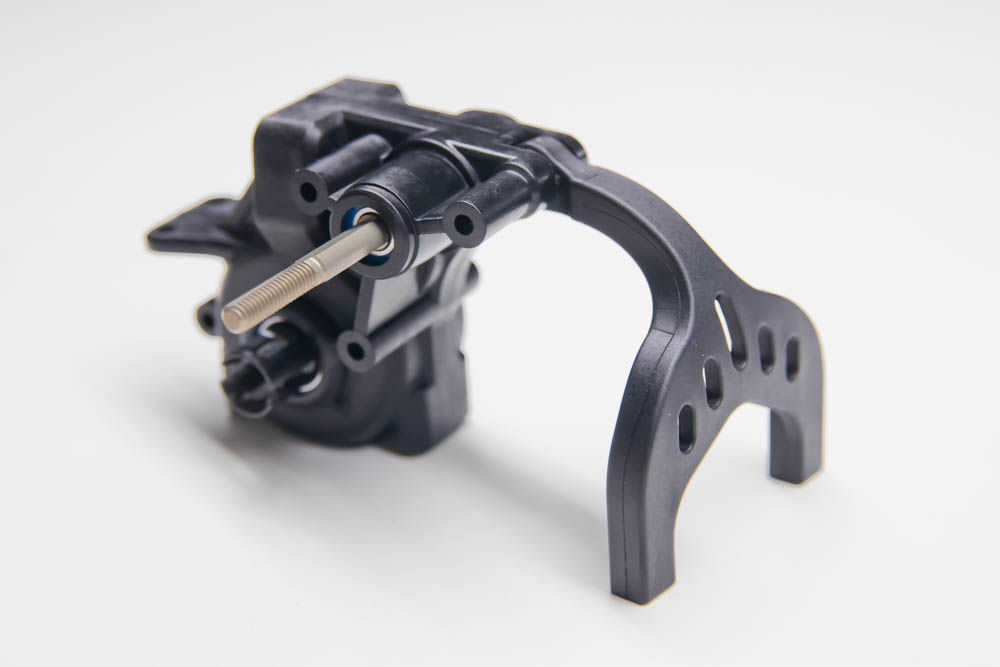
Four 3x14mm button head screws seal up the tranny and attach the waterfall. The waterfall itself used a metal pivot ball to allow additional torsional chassis flex.
|
|
The lightweight milled out motor plate goes on next. I’m a fan of the plate mounting only to one half of the tranny case. It allows you to take the tranny apart without having to take apart your slipper and its settings.
|
|
The 2-plate slipper installs next. The B6D comes with a 78-tooth spur for modified motors and a 72-tooth spur for stock. I put a dab of black grease on the 78 spur to hold the slipper pads in place to make installation easier. The manual has you set the lock nut flush with the top shaft to initially set the slipper. Final setting can be one once you’re ready to run.
|
|
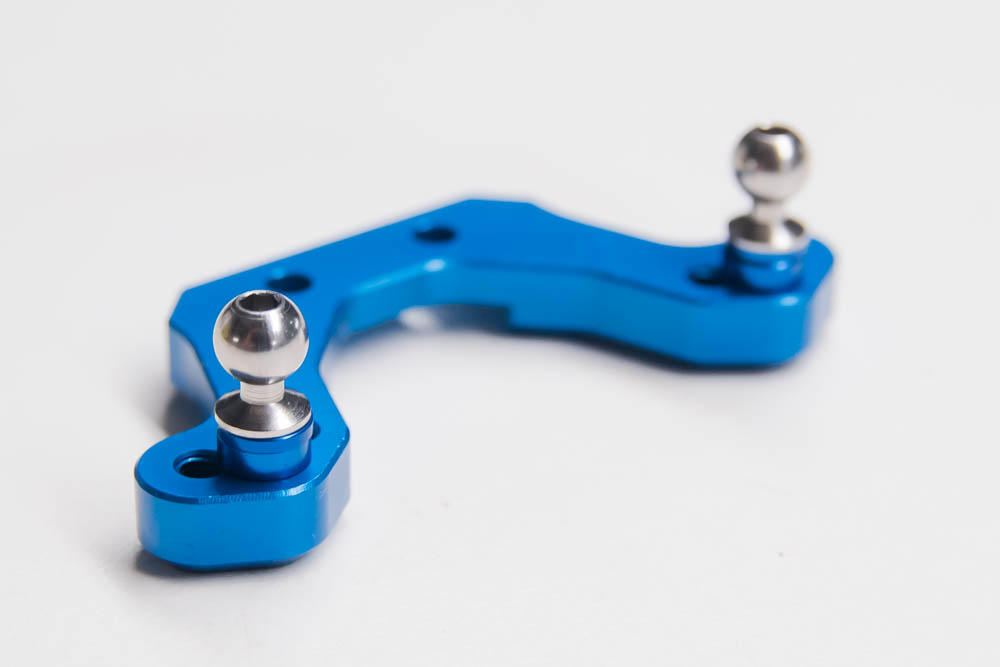
The blue aluminum rear ball stud mount preps next by mounting 3mm’s worth of blue aluminum washers underneath the ball studs. This mount will sandwich between the rear end of the tranny case and the anti-roll bar mount.
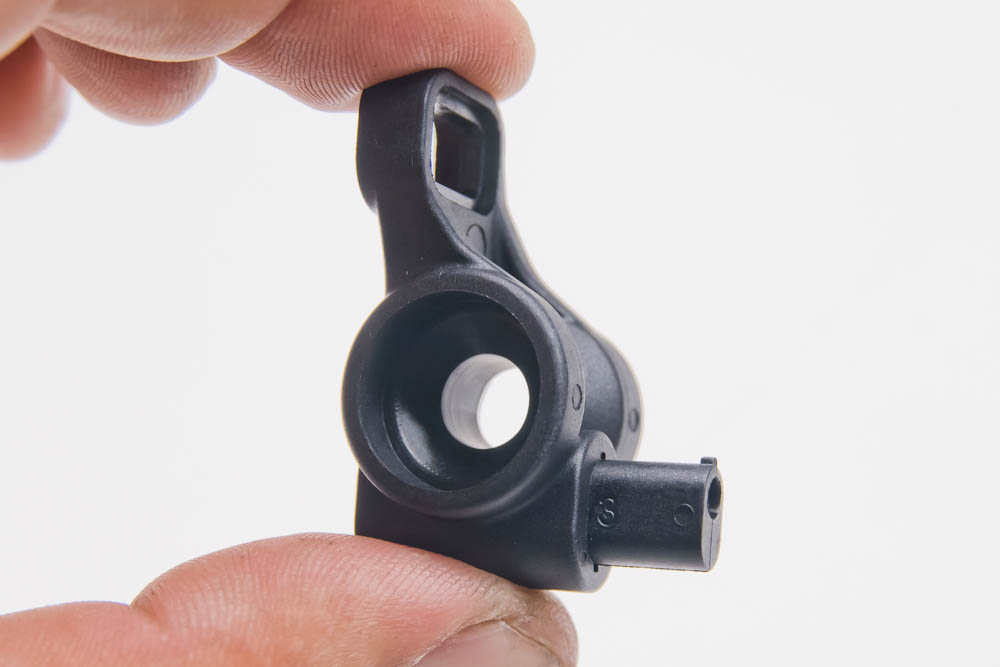
The rear hubs adjust the similar to front. Plastic inserts adjust the hub’s height to compensate for lower ride heights when running on high traction surfaces like carpet. It prevents too radical suspension arm, drive shaft angles and roll center changes from occurring. Stock setting is with the tab up on the insert.
Black grease lubes the CVA axles when they go together.
|
|
The axles ride on ball bearings and are secured in place with blue aluminum hexes with a 7mm offset.
|
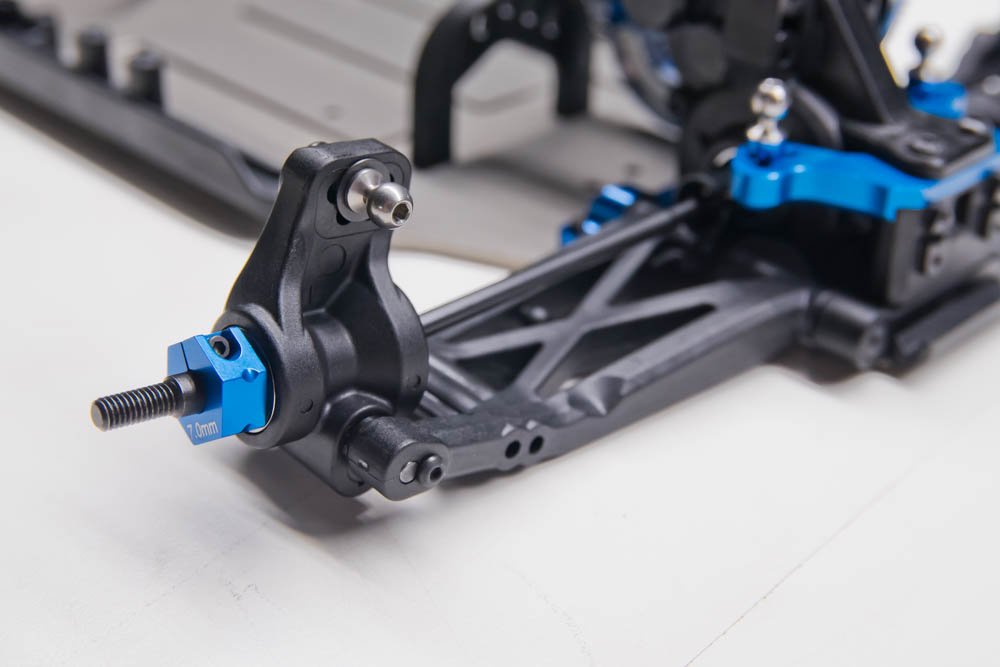
The hubs mount to the rear arm with a spacer in the front and rear of them. The hinge pin is held in place with a small button head screw.
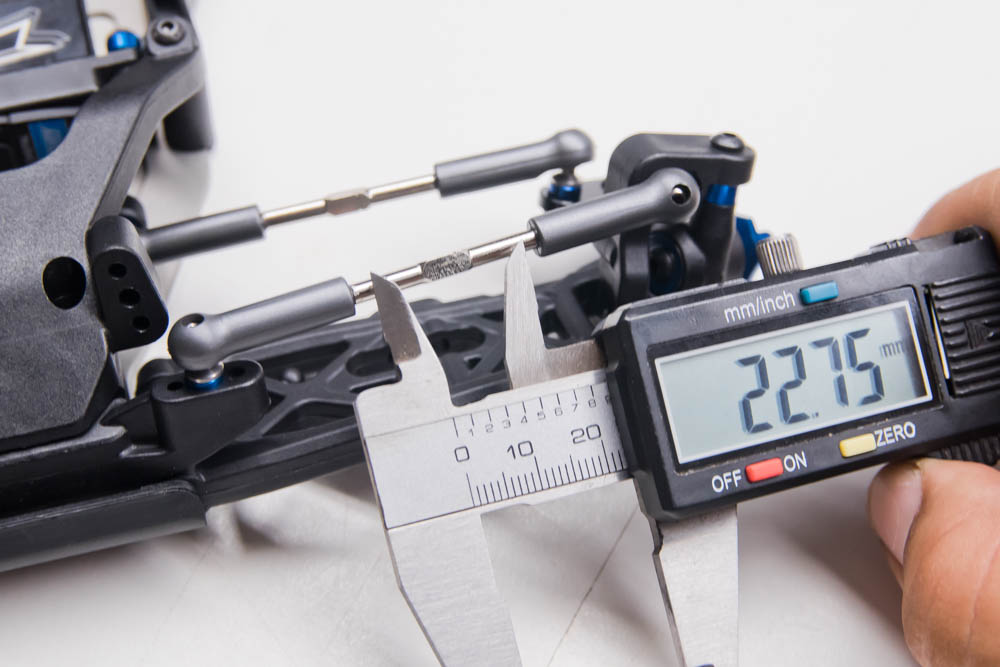
When it came time to put together the camber and steering links, I put a small dab of grease in all the ball cups where the turnbuckle threads in. Then I assembled them all the same, screwed in the ball cups until they were reach the smooth section of the turnbuckle. Mounted all the links on the car then with digital calipers an using my turnbuckle wrench, adjusted each link to the length the manual suggest.
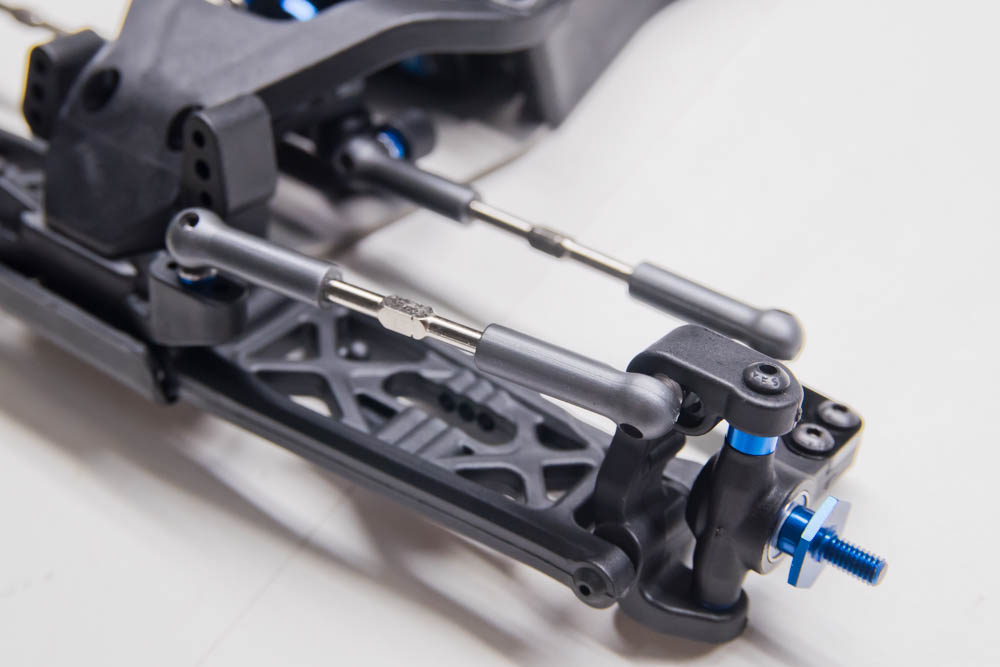 All the links looking nice once they were adjusted to the correct initial length.
|
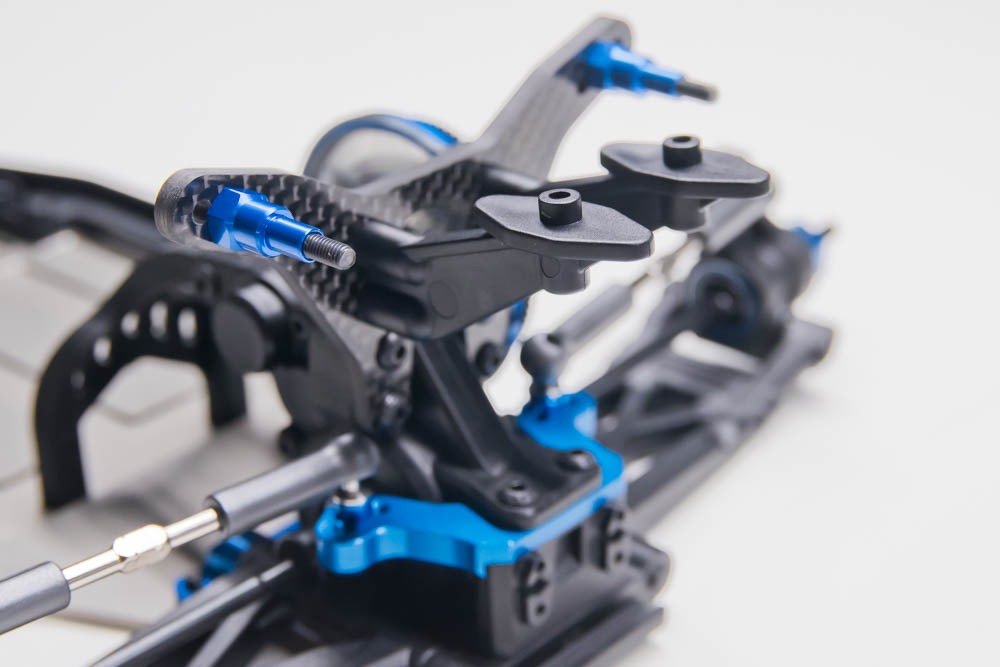
The front shock tower mounted to the top plate with four countersunk screws. The shock mounts are initially set to the middle hole on the tower.
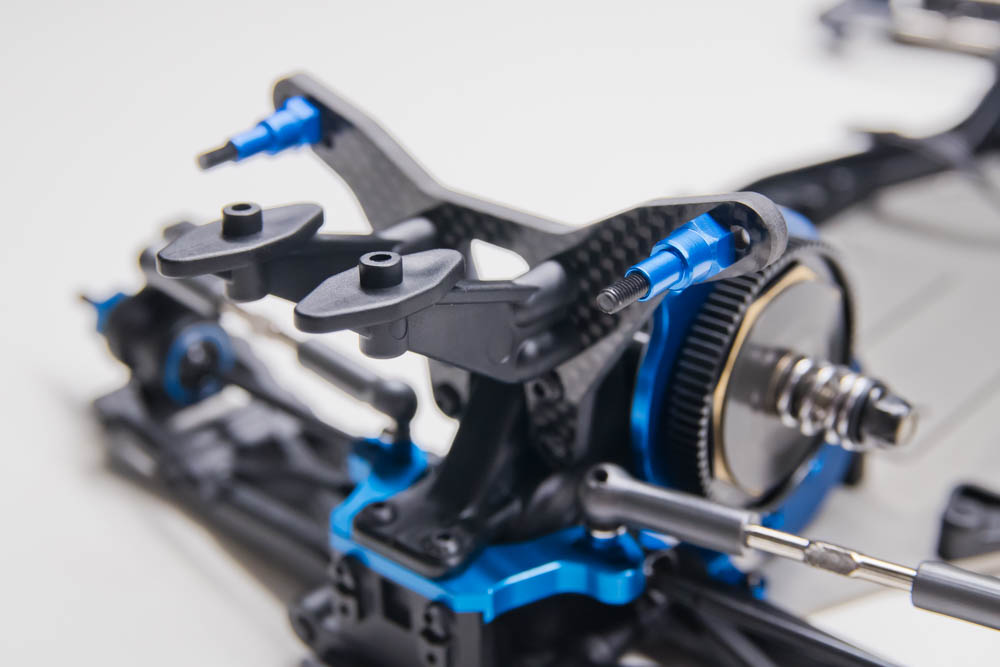
The rear shock tower mounts the same way to the back of the transmission case. The shock mounts are mounted to the middle hole on the tower. Four screws hold the wing mounts onto the shock tower.
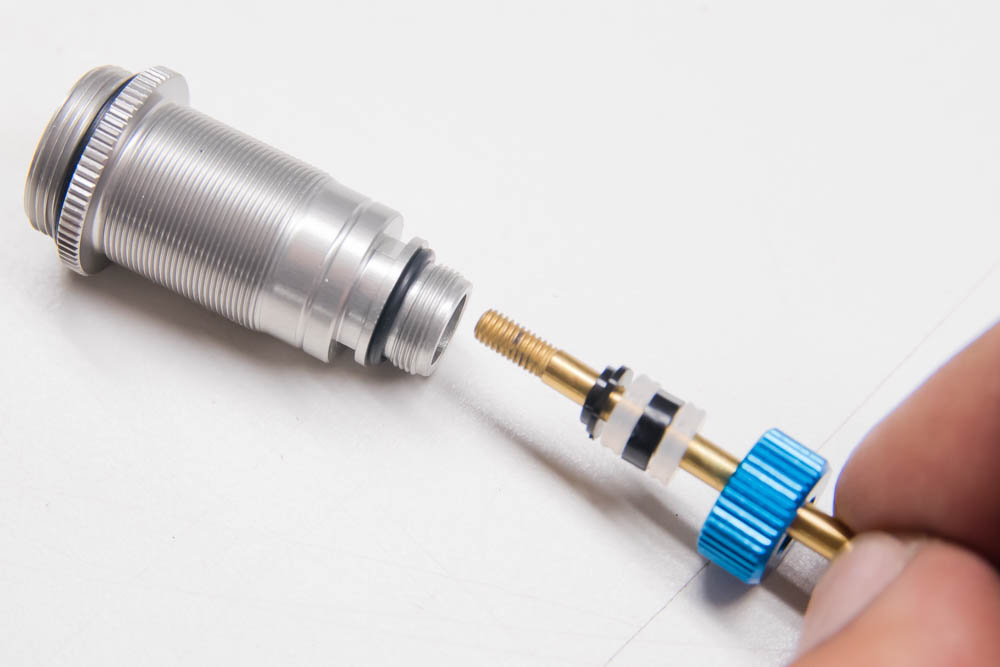
When I build shocks, I always find it easiest to mount the o-ring assembly and end cap backwards on a shock shaft and put a drop or two of shock oil to easily insert it into the shock body. Everything goes together nice, straight and quickly.
I always let my shocks sit at least 15 minutes to let all the air bubbles in the oil to work themselves out.
|
|
The shock bleeding process was simple and quick using the small bleed screw located on the plastic end caps.
|
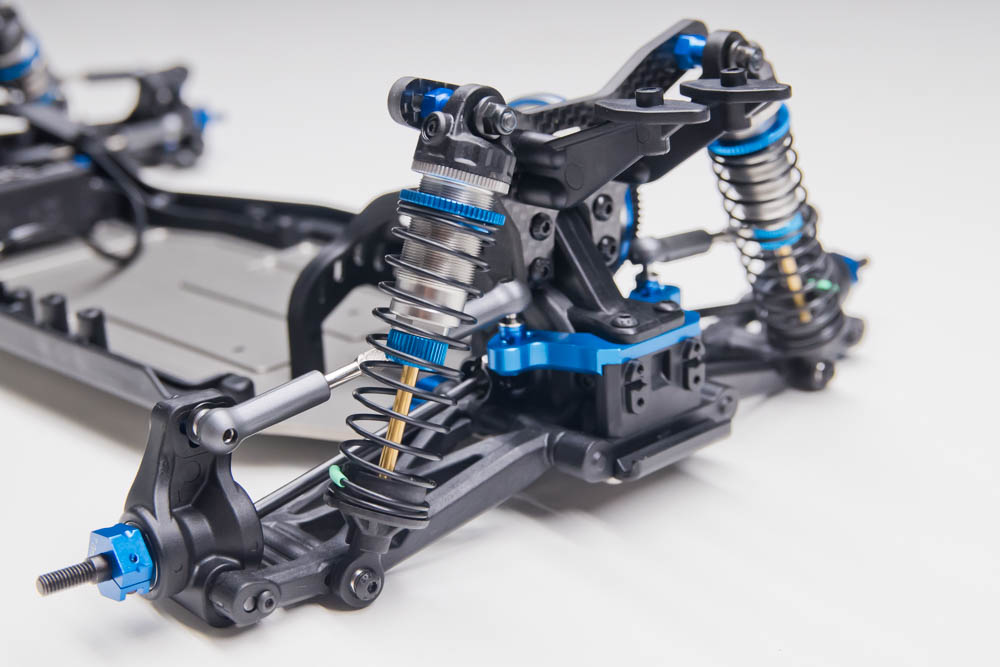
The rear shocks mount to the suspension arm inside hole using the short eyelet on the shock shaft.
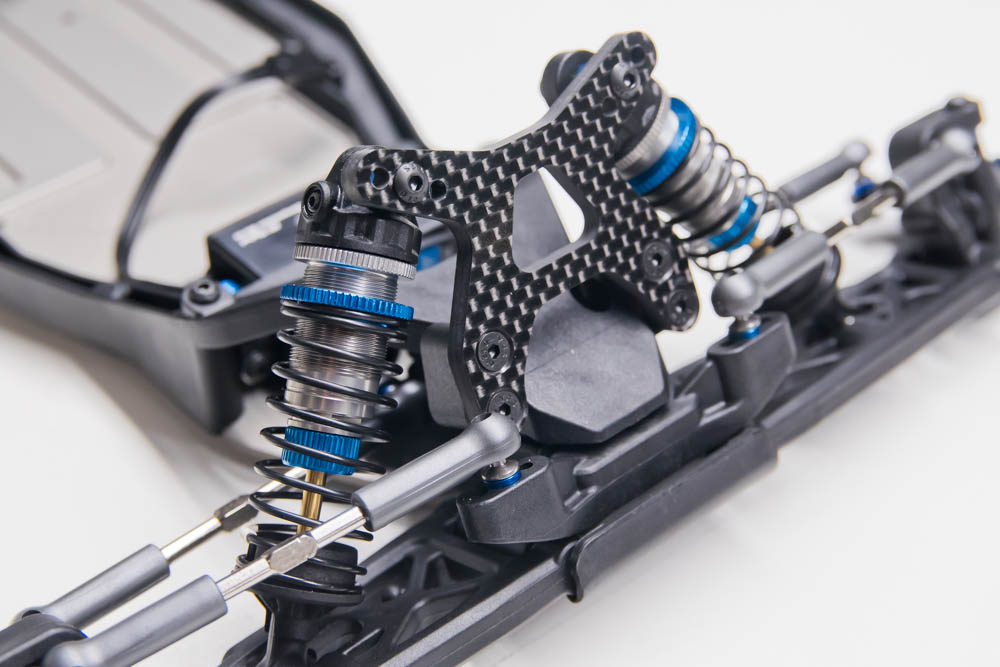
The front shocks mount to the suspension arm’s outside hole using the LONG eyelet on the shock shaft.
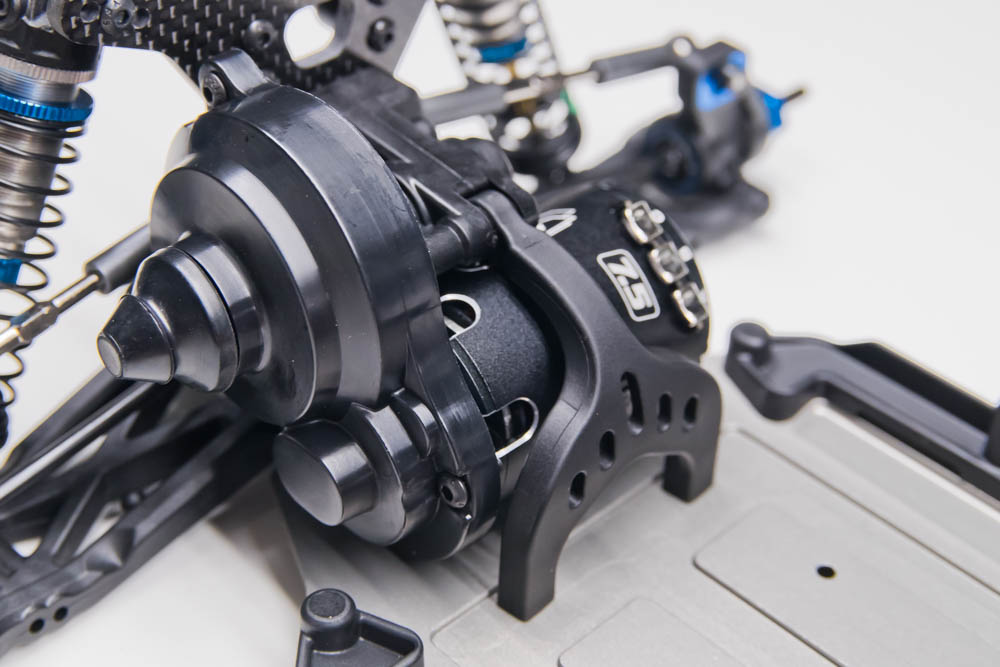
The motor and gear cover are installed next. Initial testing will be done with a 7.5-turn modified motor. But I suspect my B6D will spend most of its time racing in stock.
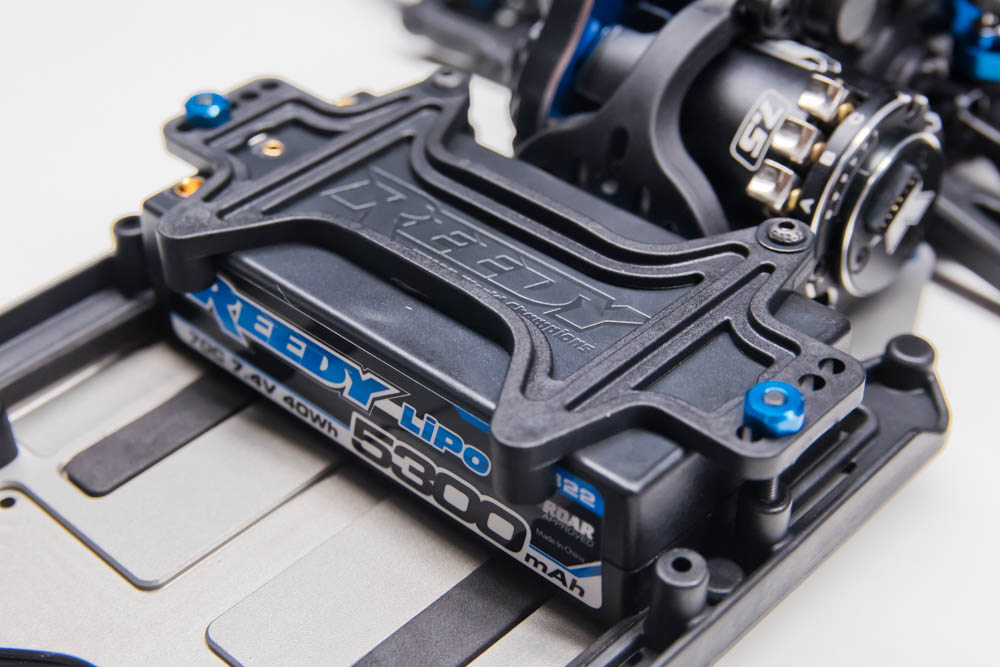
The battery mounting system on the B6D is pretty versatile. The steel battery strap shoulder screw is adjustable for multiple battery pack heights and has a forward mounting hole for the laydown transmission and rear mounting position for the stand up transmission. The battery strap incorporates multiple mounting holes to fine tune the batteries position and effect it will have on the weight bias.
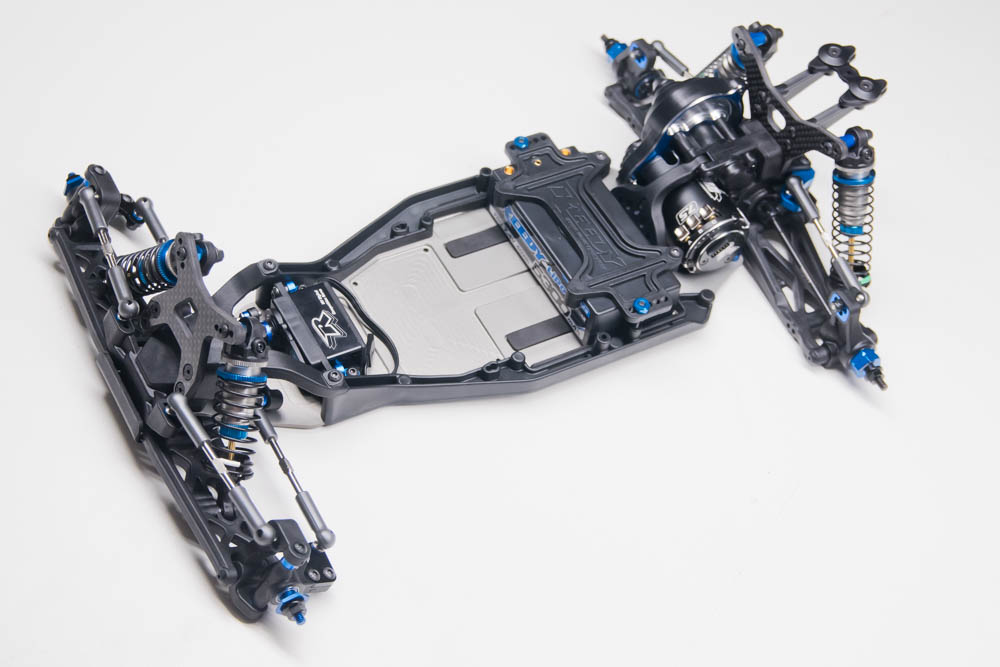
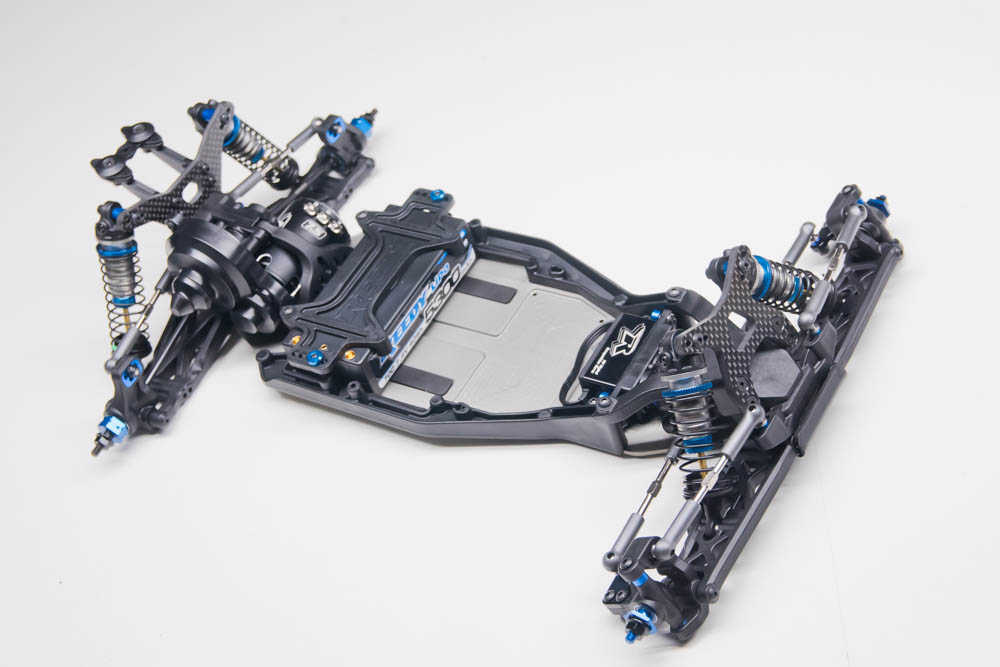
Voila! There you have it folks. The B6D is almost ready for action, it just needs to be wired up. The body is off being painted by Charlie V at CBuilt Designs and wheels and tires are being supplied by Pro-Line. Look out for the B6 and B6D dual review in the November issue of RC Car Action. Stay tuned!
Sources Team Associated & Reedy Electronics: Team Associated
|