Dynotest:
Team Orion Formula SV2
Words: Steve Pond
BUSHINGS
OR BEARINGS? SV2s are machine-wound, modified
motors designed for budget-conscious racers and
bashers. Team Orion created two lines: the Pro Bushing
(Pro) and the Pro Ball Bearing (Pro BB). Pro motors
are less expensive, but they give up features so they
can be offered at the lower price. Besides using
bushings to support their armatures, their endbells
are fixed. Pro BB motors feature adjustable timing and
removable endbells. Both versions come with bullet
connectors installed, so their installation in most
RTR vehicles doesn’t require soldering.

ENDBELL. The SV2’s endbell is the motor’s
most significant feature. Its molded section is very
similar to that of the endbells on Orion’s Core
motors, but the brush hoods that house their brushes
and springs are stamped into a triangular shape. The
brushes are inserted into the center of the brush hood
and contact the commutator at a 45-degree angle. The
top of each brush hood features an area where the
brush shunt can be hooked. This feature allows the
brushes to be pulled out of the way when you remove
the endbell for maintenance. The brushes and the brush
hood make less contact than the V2’s the round brush
hoods, so the SV2’s brushes may not be supercooled
as they are in the V2. The angled brush hoods reduce
brush bounce just as they do in the V2.
|

Above:
The SV2’s endbell is molded with stamped brush hoods.
There’s less contact between the brushes and brush
hoods, so the brushes are cooled as much as they are
in the aluminum endbell of the V2 motor. The angle on
the brushes still prevents brush bounce.
|
Above:
The motor can and magnets are common stock in the
Orion and Peak motor lines. The can features vents in
the gap between the magnets and in its base; they
allow a good airflow when the motor is mounted against
a flat plate.
|
Above:
The wire on the Formula armature is machine-wound, so
it isn’t as pretty and as tightly wound as the
armature on hand-wound high-dollar modified motor, but
it costs much less.
|
Above:
The armature is stamped for clear
identification, and the unique cutouts in the
poles’ crowns are for balancing.
|
MOTOR
CAN.
The black motor can used for both types of
SV2 motors is very similar to those on the V2 and Core
motors. It features diagonal vents between the magnets
and four pie-shaped vents in the bottom of the can.
The vents allow air circulation even when the motor is
mounted against a flat surface. A different can is
used on the bushed Pro motors because they feature
fixed timing. Their endbells don’t have timing
rings, so there aren’t any ring retainers punched
into the can; instead, they have an endbell that’s
indexed to a slot in the motor can, and tabs secure
the endbell. That fixes the motor timing, and that can
be a good for beginners who aren’t familiar with
adjusting motor timing and want an inexpensive but
faster motor; this motor couldn’t be more “plug
and play.” The timing is set to a conservative 6
degrees, and that produces better performance than
zero timing, but it still allows safe operation in
reverse. The motor can in the Pro BB version is more
typical of a standard modified motor. It accommodates
a timing ring and allows quick endbell removal and
installation and timing adjustment.
ARMATURE. SV2s use the same armature as those
in Team Orion’s Orbital modified motors. It features
straight-stacked laminations with a full crown for
maximum torque. The armatures are all balanced, even
in the Pro versions, and they feature a unique method
of balancing. Typically, you balance armatures that
are not epoxy-balanced by drilling material from their
crowns. When the armature needs a lot of material
removed, the drill holes sometimes go deep into the
web of the armature. If the drill holes aren’t
properly centered on the web, the crown section of the
laminations can separate from the armature and damage
the motor. Orion cut material away from the armature
using the edge of a circular cutter to leave shallow,
semicircular cuts in the crown instead of thin, deep
holes. The result is a balanced armature with far less
risk of motor damage caused by drilling a balancing
hole that isn’t quite in the center of the web.

The wire isn’t wound on the armature as nicely as it
is on the hand-wound modified motors. This isn’t
unique to these motors; most machine-wounds give up a
little in the winding department. The wire is quite a
bit thinner, and as a result, there’s a little more
resistance through the windings. There’s plenty of
room for a wire of a heavier gauge that would bump up
the ponies, but remember: these are machine-wound
motors; using big, burly wire isn’t an option.
Available
winds

Available
Formula SV2
Pro Winds

ORI21035: 10x2
ORI21036: 11x2
ORI21037: 12x2
ORI21038: 13x2
ORI21039: 14x2
ORI21040: 15x2
ORI21041: 17x2
ORI21043: 19x2
ORI21044: 21x2
ORI21045: 23x2

Available
Formula SV2
Pro BB Winds

ORI22031: 10x1
ORI22032: 10x2
ORI22033: 11x2
ORI22034: 12x1
ORI22035: 12x2
ORI22036: 13x3
ORI22037: 14x2
ORI22038: 15x2
ORI22039: 17x2
ORI22040: 19x2

Available
brushes
ORI41330: SV2 brush (41092)/spring
(41392) assembly with eyelet
ORI41910: round,
Enduro-compound
ORI41091: round,
Sprint-compound
ORI41092: Edge Enduro-compound
ORI41093: Edge Sprint-compound
brushes

Available
springs
ORI41390: soft, 11-coil,
0.30mm
ORI41391: medium, 10-coil,
0.30mm
ORI41392: medium/hard, 9-coil,
0.30mm
ORI41393: hard, 8-coil, 0.30mm
ORI41386: 10-coil, 0.35mm
ORI41387: 9-coil, 0.35mm

|
DYNO
TESTING RESULTS
|
10x1
BB OUT OF THE BOX

Peak rpm: 45.561

Peak power (watts):
185.3

Peak torque (Nmm):
152.6

Torque @ peak power
(Nmm): 82.9

Peak efficiency: 69.1%

10x1
BB TUNED

Peak rpm: 49,001

Peak power (watts):
221.1

Peak torque (Nmm):
174.8

Torque @ peak power
(Nmm): 89.7

Peak efficiency: 74.5%

13x3
BB TUNED

Peak rpm: 37,854

Peak power (watts):
211.6

Peak torque (Nmm):
209.2

Torque @ peak power (Nmm):
107.4

Peak efficiency: 80.2%
|
|
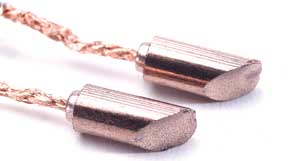 |
|
Left:
Enduro-compound Edge brushes
are standard in all Formula
Pro motors. They’re flat on
each side to give a slightly
better throttle response than
fully round brushes. |
Left:
The unique brush springs are
wound to taper down towards
the brush. The large coil
diameter at the top helps to
prevent the springs from
coming out through the top of
the brush hood.
|
BRUSHES.
SV2 motors come standard with
SV2 brush/spring assemblies—Enduro-compound
Edge brushes and medium/hard
springs. As the name implies,
the Enduro-compound brushes
last longer than others in the
V2 brush lineup. According to
Team Orion motor guru Cliff
Black, the Edge brush
configuration features flat
sides instead of being
completely round like a
standard brush, so Formula
motors have a little more
punch than they would if they
had standard brushes.
According to Black, the blunt
face of the brushes energizes
the segments of the commutator
more quickly, and that gives
the motor a little extra snap.
BRUSH SPRINGS. Round
brush springs are part of what
makes the V2 and SV2 motors
unique. The springs latch into
the triangular brush hoods and
apply straight, even pressure
on the brushes for more
consistent contact with the
commutator. I did have trouble
with one of the brush springs
that didn’t want to be
installed securely; it kept
springing out of the top of
the brush hood. As it turned
out, its top coil had been
wound a little too tightly; a
little tweak with needle-nose
pliers enlarged the top coil
enough to keep it engaged with
the brush hood. The angle of
the brush hoods makes it
harder for the brushes to
bounce off the commutator at
high speed, so the SV2 uses
less spring tension than a
conventional brush spring.
That could translate into less
commutator and brush wear.
|
DYNO
TESTING
I
tested the Formula modified
motors on our Robitronic
Pro-Master dyno. The dyno is
set to a standard 7.5 volts to
simulate a 6-cell battery
pack; then I run the motors. I
allow sufficient time between
tests to ensure that the motor
is at ambient temperature at
the start of each test.
With just a little TLC,
Formula motors can be strong.
On average, the 10-turn, Pro
BB pumped out 185 watts of
power; that’s strong but not
10-turn strong. I gave the
motors a little bit more time
to break in, and then I
adjusted the timing and
applied just a little bearing
oil and comm lube. The 10-turn
then peaked at 221 watts, and
torque shot up by more than 20
percent. Both versions come
with a little advanced timing
that increases performance,
but the Pro BB is fully
adjustable.
I turned the 10-turn motor up
to about 15 degrees of timing,
and that seemed to be the
sweet spot for this motor.
Surprisingly, the Pro motors
ran as well as or better than
the Pro BBs. A 10-turn,
double-wind Pro pulled off a
pass at just over 225 watts
with stronger torque. It just
shows that when they’re
fresh, motors with bushings
can run as well as those with
ball bearings. Over time, the
bearings offer a clear
advantage, but there isn’t
any doubt that you can be fast
with a bushing-equipped
Formula Pro.
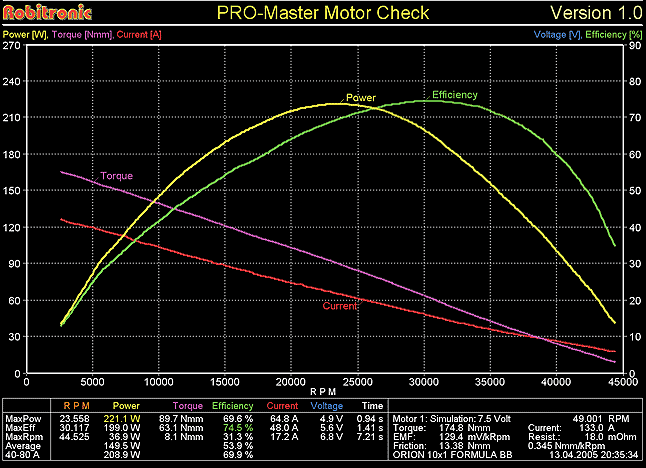
A
little commutator lube and
increased timing bump up the
power in Formula Pro motors—by
about 20 percent in some
cases. This 10-turn Formula
Pro budget bearing motor
produces very good power for a
motor of this price. Its power
is within just a few percent
of a full-blown V2 hand-wound
modified’s.
TEST-SETUP
SPECS
|
Wind:
10-turn single
Pro-Bearing

Brushes: Edge
Enduro-compound brush

Springs:
medium/hard, 9-coil,
0.30mm

Comm diameter:
0.296 in. (7.52mm)
|
|
|
|
|
|
|