

In effort to provide the best handling and fastest cars on the
track, Specialized RC presents this documentation on HOW TO BLUEPRINT YOUR
RDX. The RDX out of the box is able to perform at the highest levels of
competition. If you are looking for that last extra bit of performance then read on. The following are some tips and tricks our team use to increase the performance you have come to expect from the
RDX.
|
Bulkheads
The RDX
drivetrain is super smooth and free out of the box. If you are
looking for that last extra bit then read the tips below that
we do to make our cars perform at their best on the track.
Always wear safety glasses when using power tools. Be sure to
click on images for close up views.
-
Insert
the bearing holders in the down position and check
for tightness on them. They should slide in and
out with ease to prevent the bearings from being
pinched once inserted into the bulkheads.
-
If
the holders are tight you will want to dremel the
bulkheads a bit. Due to molding tolerances on the
bearing holders this is sometimes necessary.
|
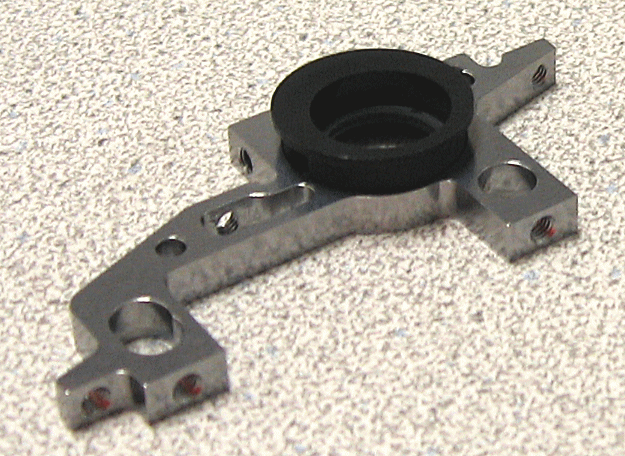
|
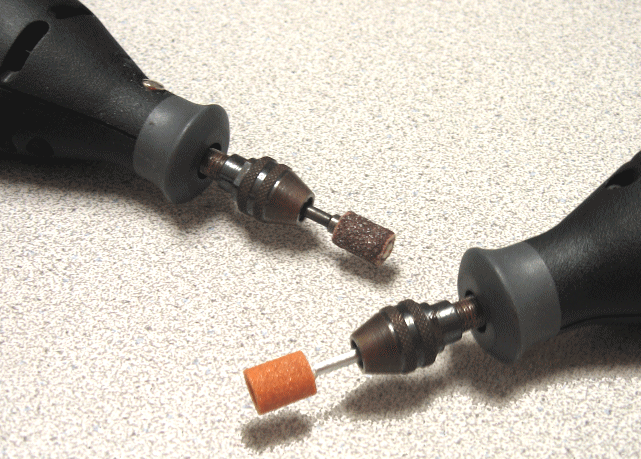
|
-
You
will want to start with a coarse bit if the
holders are tight to help in the process. Then go
back with a smooth bit to finish it off. Alternate
holding the bulkheads side to side to keep the
dremeling even.
-
Be
sure not to remove too much material, this can
cause the holders to rock too much in the
bulkheads. Do not dremel the notches.
|
-
Once
completed you will have a matched set of bulkheads
to holders. Do not mix them up otherwise they may
not fit as smooth.
-
Once
complete you will want to spray everything down
with Motorspray to remove dust and debris. Check
holders one final time with bearings installed.
|
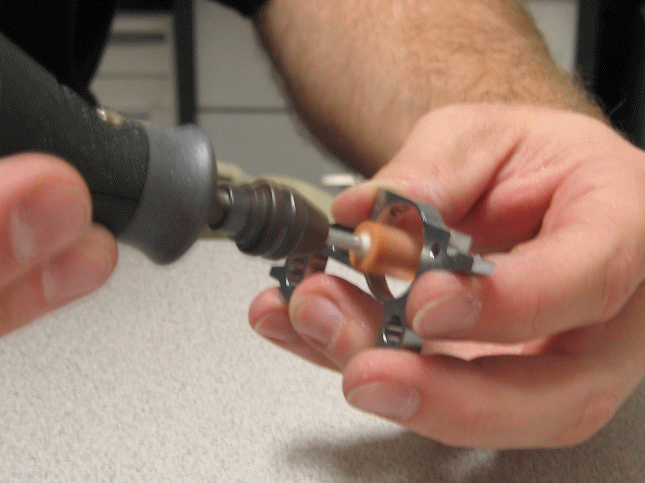
|
REBUILDING
TIPS If rebuilding a car, be
sure to check all bulkheads on a piece of glass for flatness.
Glass will be the only true flat surface unless something is
ground down to tolerance. Check the bearing holders for dirt
and tire dust buildup behind the bearings. Clean out the
corners with an X-acto knife to insure they sit down in.
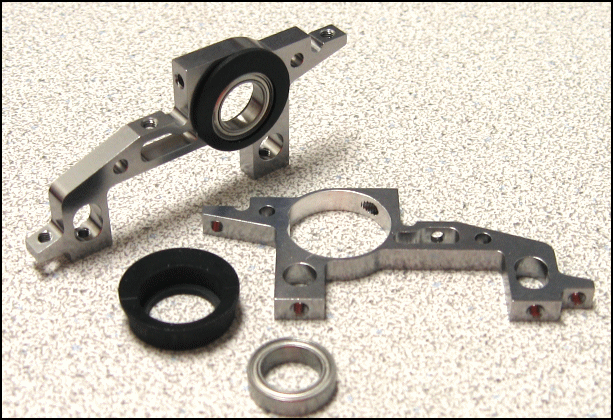
|
Differentials
The Diffs in the
RDX are smooth as glass when built up properly and follow a few
simple things. The following steps will ensure you get the silky
diffs you are looking for and perform perfectly. The diffs put
the power to the ground so we do not recommend skipping any of
the steps and make sure the parts are always in top notch
condition. Be sure to click on images for close up views.
-
The
biggest upgrade we recommend is swapping the stock
diff balls for either Carbide
(COR1011) or Ceramic
(COR1010) balls. It will vastly improve the
longevity of your diffs between rebuilds.
-
When
assembling the diffs there are 4 beveled washers
that are put onto the diff bolt. We recommend a
different pattern for placing them onto the bolt. We
recommend one face down, then two facing each other,
then the fourth washer facing upward. We feel this
prevents any possible slanting of the washers on the
bolt.
|
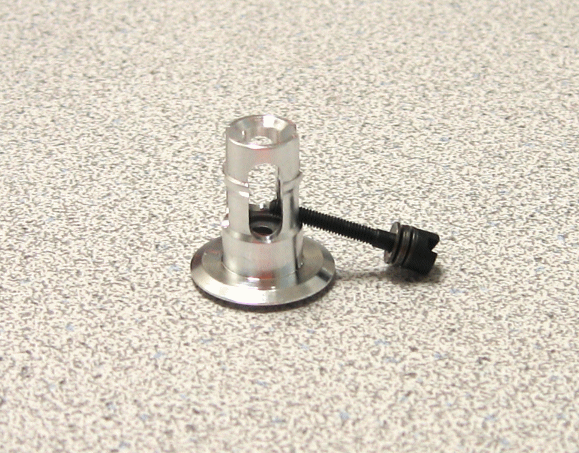
|
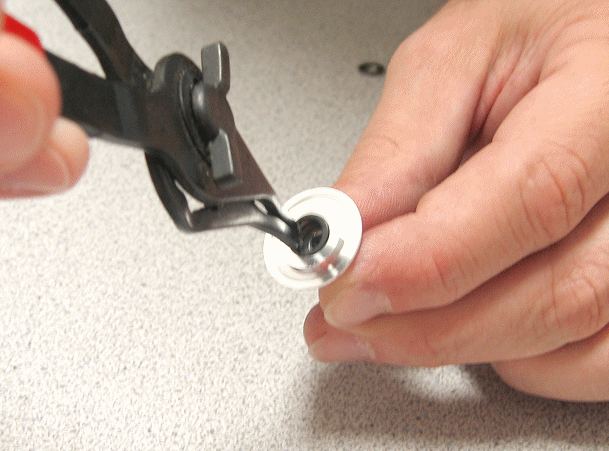
|
-
Remove
the snap ring from the short diff hub. Do not pinch
the snap ring closed otherwise it will cause
premature fatigue and give you other problems. Pinch
it enough to pull it out and no more. After 2 or 3
times of removing the snap ring you will want to go
ahead and replace it as it will fatigue.
-
Take
out the thrust bearings and clean everything down
with motor spray. Check the groove on the diff hub
where the snap ring sits for any wear marks or
debris.
|
-
The
thrust washers are two different diameters, so be
sure to put the smaller one in first. Coat the
washer with black grease, insert the thrust bearing,
coat the bearing with more black grease. Install the
final thrust washer and use the back of an X-acto
knife to seat the thrust assembly.
-
Before
installing the fresh snap ring, be sure to examine
the ring as there is a flat edge side and a more
rounded edge. You will want the flat edge side
facing outward so it locks into the groove better.
|
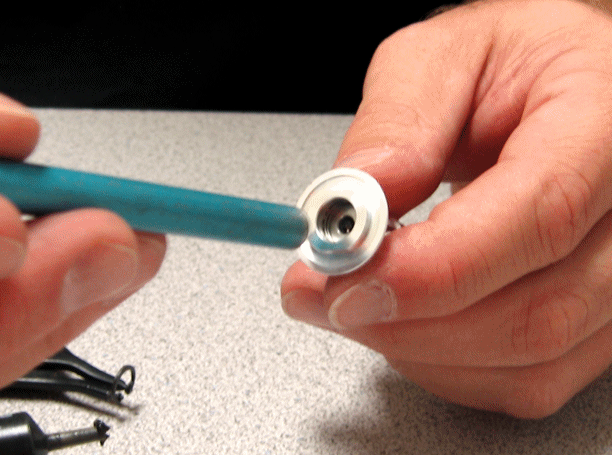
|
-
Reinstall
the snap ring into the diff, making sure not to
pinch the ring too tight. You can make sure the snap
ring is seated into the groove by pushing into the
hub with the back of an X-acto knife. You can then
check to make sure the snap ring spins freely inside
the groove with the blade of the X-acto. Finally
remove any excess black grease from the diff hub by
pushing a wrench through the middle.
|
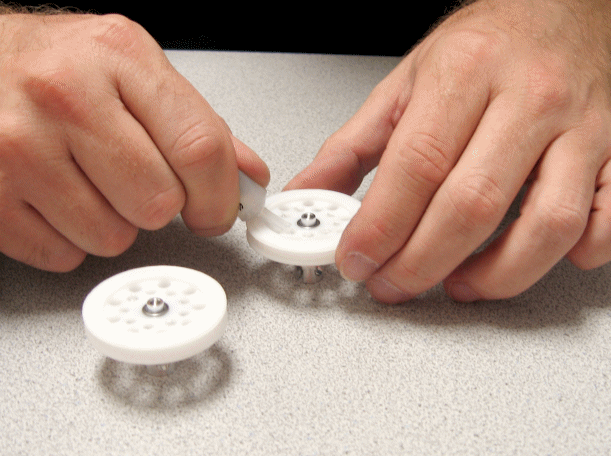
|
-
You
will now want to apply a bit of diff grease to the
diff hubs to help hold the rings on. Coat the diff
rings with diff grease before placing the pulley
onto it. Fill each of the diff ball holes with diff
grease and then insert the diff balls.
-
Next
place the other diff hub onto the pulley. Apply a
dab of loctite to the diff bolt before inserting
into the diff hub. Tighten the diff bolt until the
slop is removed and the diff is held together, do
not tighten any further yet.
|
-
Check
the smoothness of the diff before tightening any
further. The diff will be super loose and smooth
feeling with no hang ups. If everything checks out,
then tighten the diff 1/4 turn and no more. Again,
check the diff for smooth feeling and no hang ups.
-
If
everything checks out then check the tightness with
a wrench inserted into each diff outdrive. If the
pulley turns easily then tighten the diff another
1/4 turn. Repeat until pulley is pretty much locked.
It usually does not take more than 2 or 3 of the 1/4
turns to lock the diff down.
|
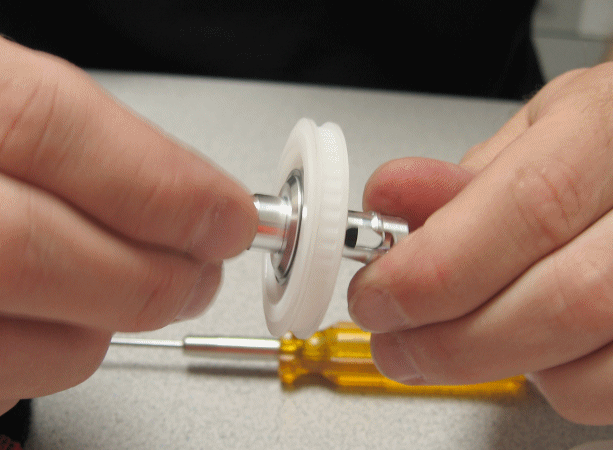
|
TIPS TO
REMEMBER If your diff develops a
high spot then you need to replace the snap ring. When replacing
the snap ring we recommend the new HD
Snap Ring (SRC79165) offered by Specialized RC.
If your diff will not tighten down and acts up no matter how
many rebuilds, then you need to check your Snap Ring and/or the
sequence of the thrust washers. Be sure to have the smaller OD
washer in first. Do not over tighten the diff bolt. You will
crush the coned washers and create other problems with your
diffs.
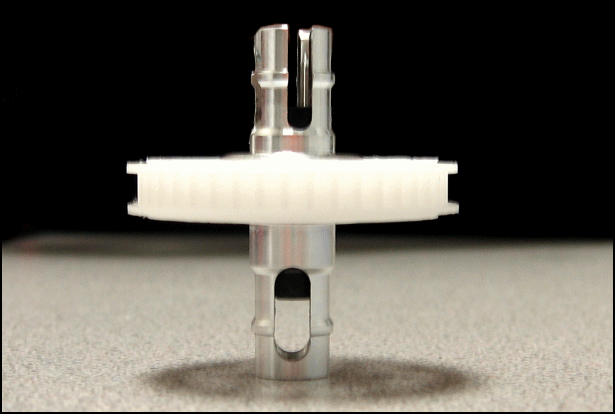
|
Shocks
Shocks need to
be super smooth to perform at their best. The tips below will
ensure your shocks are super smooth with no air gaps or leaks.
Follow these steps and you will have smooth action shocks for
a long time. Be sure to click on images for close up views.
-
When
assembling shocks, the first thing we do is
disassemble the kit shocks completely, this
includes removing the G-clip on them and pulling
out the o-rings and washers in the shock body. Be
sure not let the G-clip spring out otherwise you
may lose it.
-
The
first thing we do is replace one of the o-rings in
the shock body with a thick washer. We find the
thickest washer included in a Losi parts bag,
LOSA5050, works perfectly. The reason is to
improve the reactiveness of the shock for
transitions on the track.
|
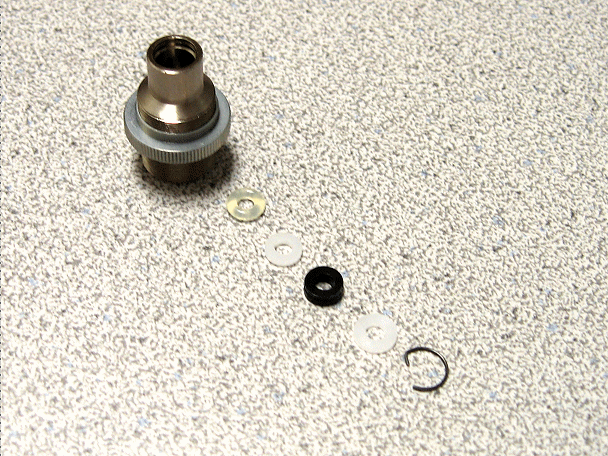
|
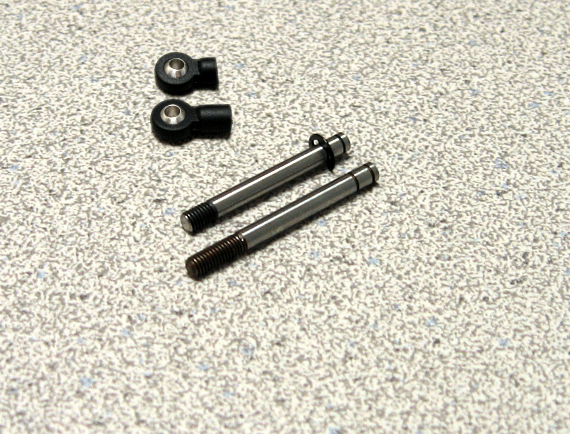
|
-
If
you are racing on carpet and are utilizing the lowered
shock tower (COR79238) you will
want to cut down the shock eyelets and shock
shafts for the front shocks. You should cut the
shock shafts down about half way, along with the
eyelet. You will be able to use the stock spring
perches once this is done. Once the shock shafts
are cleaned up with motor spray, install the
pistons you plan to use.
|
-
Before
putting the shock shaft back through the shock
body, be sure to put a drop of shock oil onto the
o-ring in the shock body to prevent any damage to
it.
-
Once
you fill the shock body and get the air bubbles
out you will want to put the bladder in seperately
from the cap. Place the bladder into the body and
it will sink down a bit. Use the back of an X-acto
knife to push it down and seal it up. You should
have a good tight seal now.
|
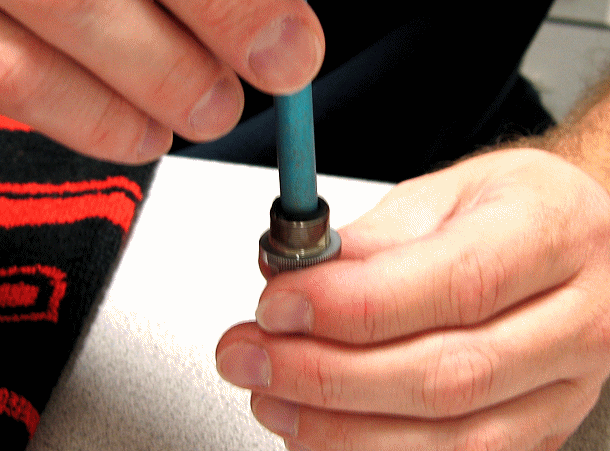
|
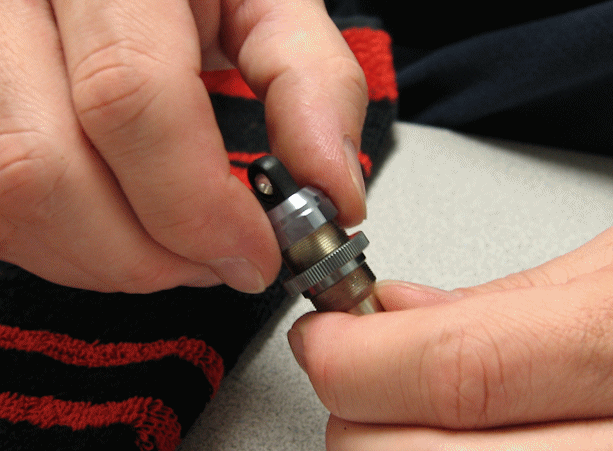
|
-
When
putting the cap onto the shock body, do not grip
the plastic part of the cap. Only let your fingers
twist on the aluminum portion of the cap.
Otherwise this is how the seal of the bladders is
broken and causes leaks once assembled. The
plastic cap may or may not turn but it does not
matter.
-
When
putting the shock eyelets back onto the shock
shafts, be sure not to crank down on them too much
otherwise they will crush and bind up the pivot
ball in the shock eyelet.
|
- Once the eyelets are installed and the shock
rebounds the way you want you will want to measure
the shocks to ensure they are the same length side
to side. Obviously the front and rears will be
different due to the lowered shock tower. If you
are using the standard front tower then all four
shocks should measure the same.
- Once the shock is done and you are putting the
springs on, if you are using any of the silver
springs you will want to crush them down once.
Using a pair of pliers as shown in the picture
helps with the stiffer springs in the package. It
will help the springs break in and sit more even
side to side.
|
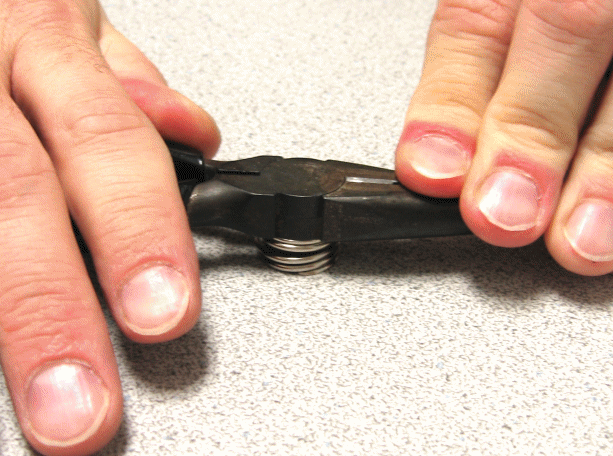
|
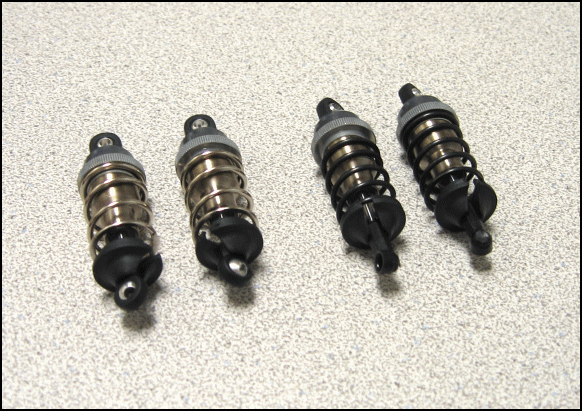
|
Source:

Banners are for your personal
interest, so use them and you will also support this website
Les bannières sont
pour votre usage personnel, utilisez-les et vous supportez ce site par la même
occasion
|